Resources
Commonly used injection molding process, you know which ones?
Release time:2023-11-10
Commonly used injection molding process, you know which ones?
As technology develops, so do the demands on the injection molding process. The choice of injection molding is mainly determined by the type of plastic, the starting form, and the shape and size of the product. Commonly used methods of injection molding include extrusion, injection molding, blow molding and calendering, each of which has its advantages and disadvantages and is better suited for specific applications.
Injection Molding
Injection molding also known as plastic injection molding, the principle is to add granular or powdery raw materials to the hopper of the injection machine, the raw material is heated and melted into a flowing state, driven by the screw or piston in the injection machine, through the nozzle and the mold's pouring system into the mold cavity, the hardening and shaping in the mold cavity.
Factors affecting the quality of injection molding: injection pressure, injection time, injection temperature.
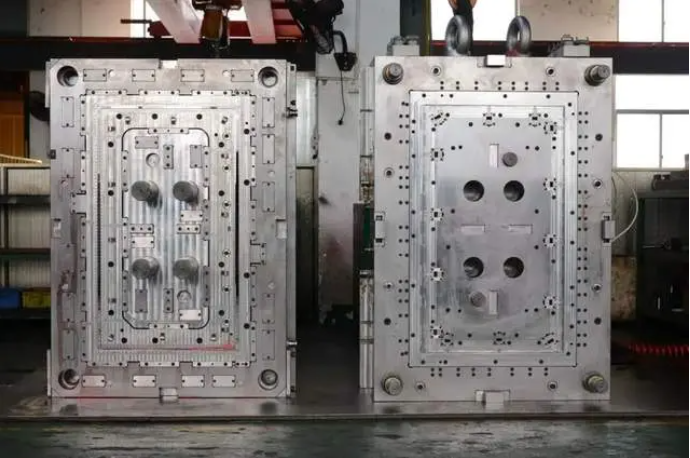
Advantages:
1. short molding cycle, high production efficiency, easy to realize automation
2. can produce complex shape, precise size, with metal or non-metallic inserts of plastic parts
3. Stable product quality
4. Wide range of adaptation
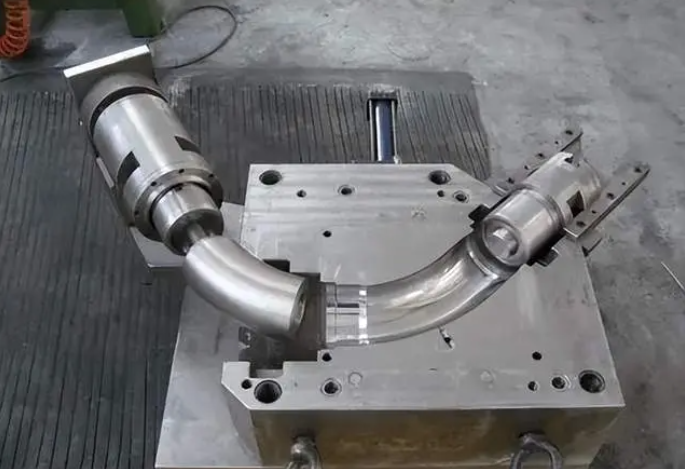
Application:
In industrial products, injection molding products are: kitchenware (garbage cans, bowls, buckets, jugs, cutlery and various containers), the shell of electrical equipment (hair dryers, vacuum cleaners, food mixers, etc.), toys and games, a variety of products for the automotive industry, and parts of many other products.
Two-color injection molding
Two-color injection molding is a molding method in which two different colors of plastic are injected into the same mold. It can make the plastic appear in two different colors, and can make the plastic parts show regular patterns or irregular cloud-like patterns, in order to improve the usability and aesthetics of the plastic parts.
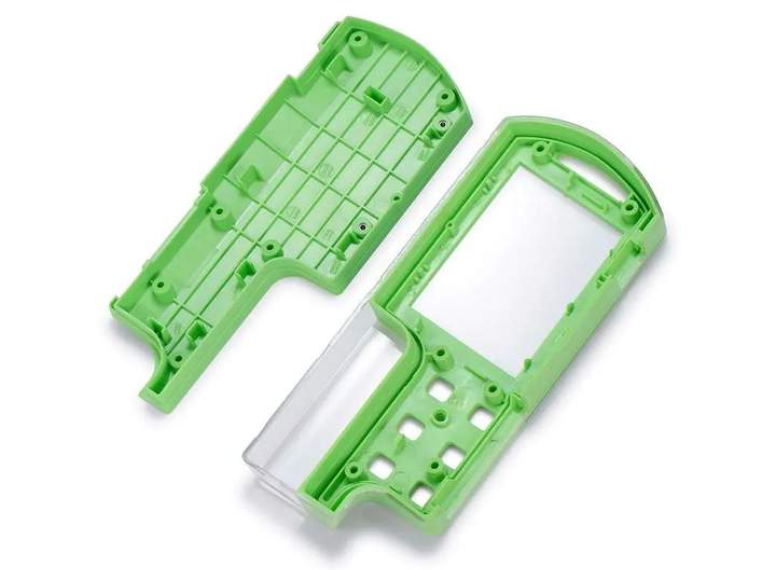
Process characteristics:
1. Core material can be used with low viscosity to reduce injection pressure.
2. The core material can be recycled for secondary use.
3. According to the different characteristics of use, such as thick parts of the finished skin material using soft materials, the core material using hard materials or core material can be used to reduce the weight of foamed plastic.
4. you can use the lower quality of the core material to reduce costs.
5. the skin material or core material can be used expensive and with special surface properties to increase product performance.
6. the appropriate skin material and core material with can reduce the residual stress of molded products, increase mechanical strength or product surface properties.
Nano injection molding (NMT)
NMT (NanoMoldingTechnology): It is a method of combining metal and plastic with nanotechnology. After the metal surface is nano-treated, the plastic is directly injection molded on the metal surface, so that the metal and the plastic can be molded as one.
Nanomolding technology is divided into two types of processes according to the location of the plastic: one is the plastic for the non-appearance of the surface of the integrated molding; the other is the plastic for the appearance of the surface of the integrated molding.
Process characteristics:
1.Products with metal appearance texture.
2. products simplify the design of institutional parts, so that the product is lighter, thinner, shorter and smaller.
3. reduce production costs and high bonding strength, and significantly reduce the use of related consumables.
Application:
General cell phone shell, laptop shell and other electronic products will be used in nano-injection molding process.
Blow Molding
Blow molding is the treatment of raw materials, placed in the folio mold, through the compressed air, so that the embryo close to the inner wall of the mold, after cooling, demolding. Blow molding is generally divided into film blow molding and hollow blow molding.
1. film blow molding
Thin film blow molding is the molten plastic from the extruder head of the annular gap in the mouth of the mold was cylindrical thin tube extrusion, while from the center of the head hole to the thin tube cavity into the compressed air, the thin tube will be blown into a larger diameter tubular film (commonly known as bubble tube), rolled after cooling.
2. Hollow blow molding
Hollow blow molding is with the help of gas pressure, will be closed in the mold cavity in the rubber-like state of the billet blown into the hollow products of the secondary molding technology, is the production of hollow plastic products. Blow molding is a method of producing hollow plastic products. There are extrusion blow molding, injection blow molding, and stretch blow molding according to the manufacturing method of the mold blank.
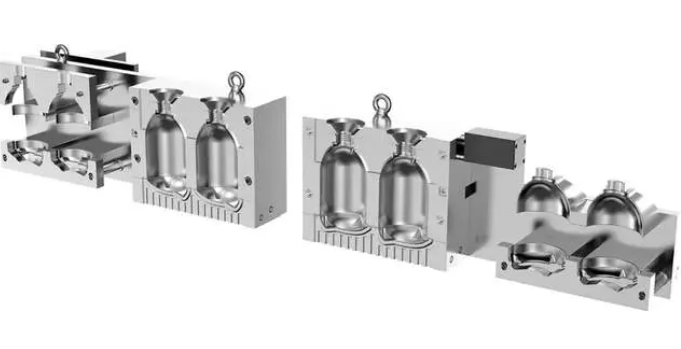
Advantages:
Product wall thickness uniformity, small weight tolerance, less post-processing, small waste edges, the production cost of the product is also lower; resistance to tensile, impact, bending and environmental strains such as higher performance, has a better use of performance, suitable for the production of large batches of small fine products.
Applications:
1. film blow molding is mainly used for manufacturing plastic film;
2. hollow blow molding is mainly used to make hollow plastic products (bottles, drums, spray cans, tanks, cans, toys, etc.).
Extrusion Molding
Extrusion molding, also known as extrusion molding, is mainly suitable for thermoplastic plastic molding, but also suitable for some of the better flow of thermosetting and reinforced plastic molding.
The molding process uses a rotating screw to extrude heated and molten thermoplastic raw materials from a head with the desired cross-section shape, which is then shaped by a shaper and then cooled by a cooler to make it cold, hard and cured to become a product with the desired cross-section.
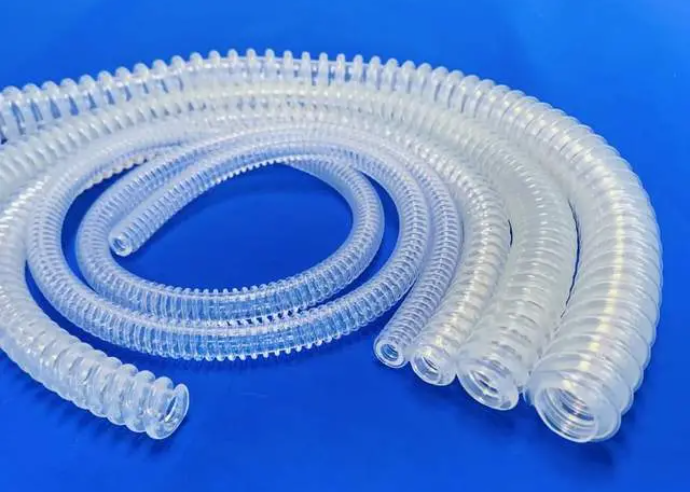
Process characteristics:
1. low cost of equipment;
2. simple operation, easy to control the process, easy to realize continuous automated production;
3. high production efficiency; product quality is uniform and dense;
4. by changing the head mouth mold can be molded various cross-section shape of the product or semi-finished products.
Applications:
In the field of product design, extrusion molding has strong applicability. The kinds of products of extrusion molding are pipes, films, rods, monofilaments, flat belts, nets, hollow containers, windows, frames of doors, plates, cable cladding, monofilaments and other profiles.
Calendering
Calendering is a method in which plastic raw materials are passed through a series of heated compression spokes so that they are joined under the action of extrusion and spreading to become film or sheet.
Characteristics of the process:
Advantages: good product quality, large production capacity, automated continuous production.
Disadvantages: Huge equipment, high precision requirements, many auxiliary equipment, the width of the product is limited by the length of the calender cylinder.
Applications:
Mostly used in the production of PVC soft film, sheet, plate, sheet, artificial leather, wallpaper, floor leather and so on.
If you have project needs, please contact us!
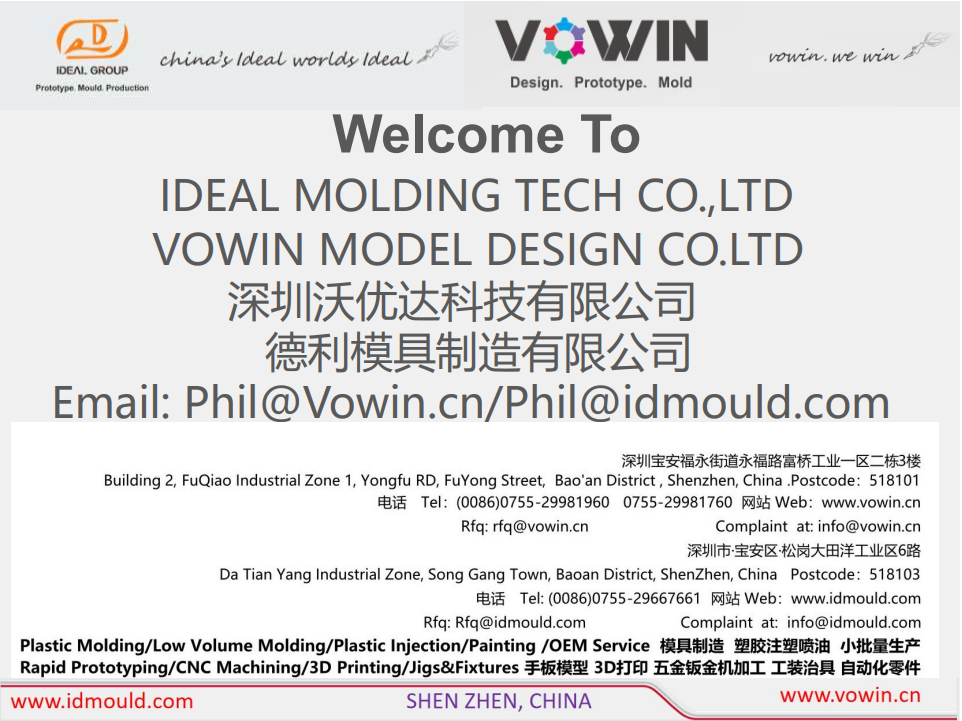
Posts by Topic
Recent Posts
- What do we need to pay attention to the plastic mold machining process and machining procedures?
- What kinds of plastic mold materials?
- What is the process of mold manufacturing?
- What should be paid attention to the polishing of injection molds?
- What is easy to ignore when maintaining and overhauling injection molds?
- What are the 6 systems of plastic molds?
- What are the methods of strengthening the surface of injection molds?
- What are the methods of insulation for injection molds?
- How to solve the problem of injection mold release difficulty?
- How can we increase the brightness of ABS injection molded parts?