Resources
What are the characteristics and considerations of the injection molded metal insert process?
Release time:2023-11-09
What are the characteristics and considerations of the injection molded metal insert process?
Insert injection molding has the following characteristics:
1. The combination of the resin's easy molding and bending properties and the metal's rigidity, strength, and heat resistance can be used to make complex and delicate metal-plastic integrated products.
2. Especially the use of resin insulation and metal conductivity of the combination of molded products to meet the basic functions of electrical products.
3. The prior molding combination of multiple inserts rationalizes the post-engineering of the product unit combination.
4. Inserts are not limited to metal, but are also available in cloth, paper, wire, plastic, glass, wood, coils, and electrical parts.
5. For rigid molding products, rubber sealing gasket plate bending elastic molding products, through the base of the injection molding made of integrated products, can eliminate the complexity of the arrangement of the sealing area, so that the automation of the combination of post-processes easier.
6. Because of the joining of molten material and metal inserts, the gap between the metal inserts can be designed narrower compared to the press-in molding method, making the molding of composite products more reliable.
7. Choose the appropriate resin and molding conditions, even for products that are easy to change shape and break (such as glass, coils, electrical parts, etc.), through the resin can be sealed and fixed.
8. Choose the appropriate mold structure, inserts can also be completely sealed into the resin.
9. Vertical injection molding machine and robots, inserts, such as the combination of the whole series of devices, insert molding project can be automated production.
10. Insert molding, after the core hole treatment, can also be made into products with hollow grooves.
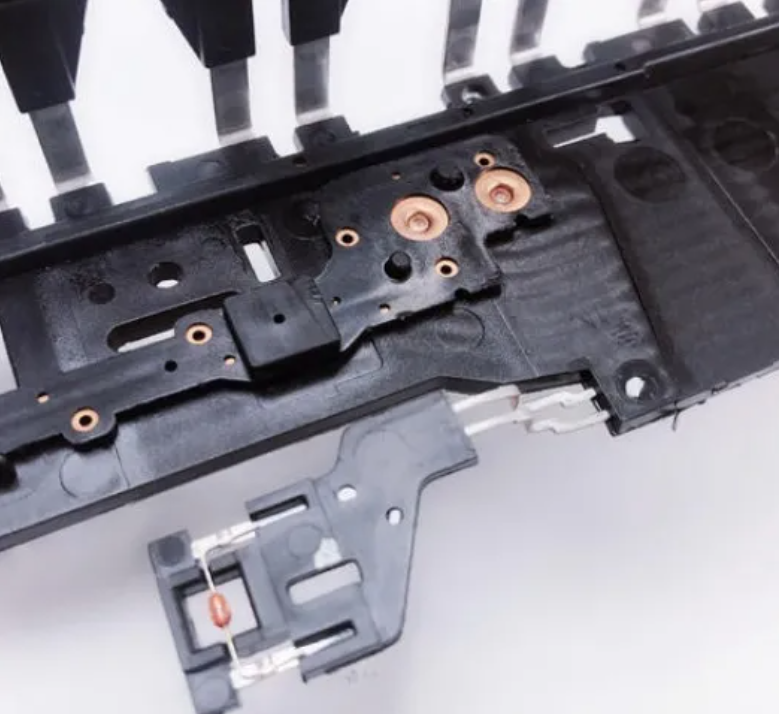
Automatic insert molding system design selection considerations:
1. Metal insert molding is prone to molding shrinkage rate is not uniform, should be done beforehand important parts of the shape, dimensional accuracy of the limit test.
2. the injection process of metal inserts are easy to deformation and displacement, should give full consideration to the composition of the mold and easy to maintain the shape of the metal insert mold design. For the insert shape can not change the product, the prior test is indispensable.
3. If the metal inserts are arranged separately and a conveyor is used, the contact between the metal inserts and the contact between the inserts and the vibrating ball may cause minor damage to the surface of the inserts, which may affect the quality of the product. The permissible limit of quality should be confirmed in advance.
4. should be measured in advance metal inserts due to stamping process caused by jagged, warping amount, material thickness difference, diameter difference, thickness difference caused by gold processing. On this basis, the automation device supporting the choice of design and mold structure design.
5. Mold gate location, molding cycle and other constraints on the mold structure of the predictable matters, as far as possible to solve in advance or have the corresponding improvement measures.
6. should confirm whether the metal inserts need preheating or drying treatment. The purpose is to ensure product quality and molding stability.
7. A variety of detection devices are set up in the mold to ensure the stability of molding action under the influence of heat, force, vibration and other environmental conditions of the mold, and it should be confirmed whether to use them or not.
If you have mold customization needs, please contact us!
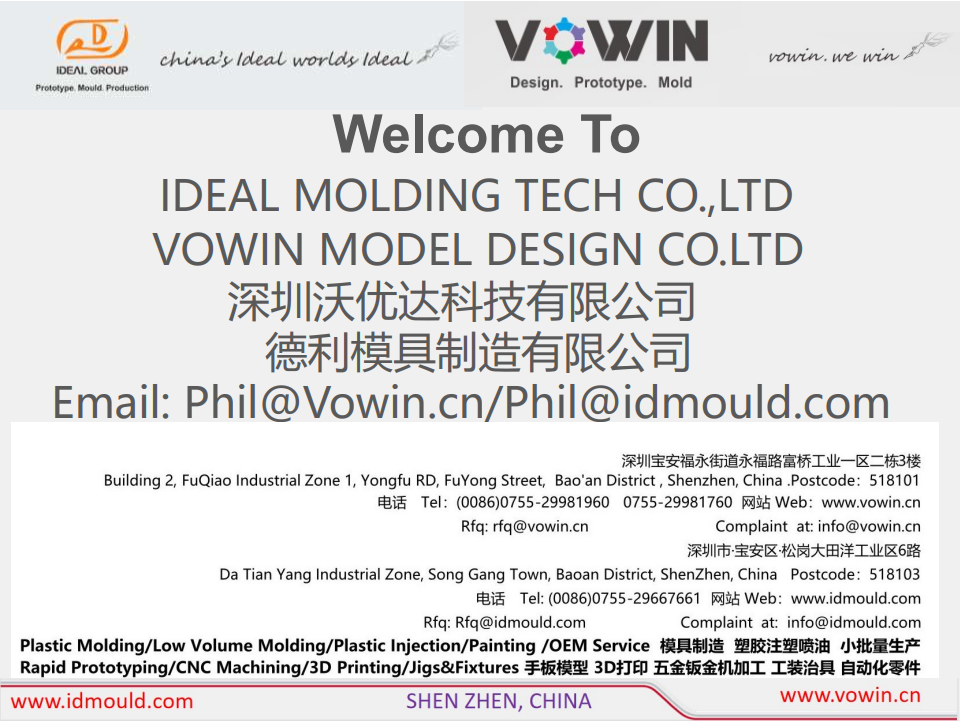
Posts by Topic
Recent Posts
- What do we need to pay attention to the plastic mold machining process and machining procedures?
- What kinds of plastic mold materials?
- What is the process of mold manufacturing?
- What should be paid attention to the polishing of injection molds?
- What is easy to ignore when maintaining and overhauling injection molds?
- What are the 6 systems of plastic molds?
- What are the methods of strengthening the surface of injection molds?
- What are the methods of insulation for injection molds?
- How to solve the problem of injection mold release difficulty?
- How can we increase the brightness of ABS injection molded parts?