Resources
What should I do if the product is not full of glue in injection molding?
Release time:2023-11-13
What should I do if the product is not full of glue in injection molding?
This is a frequently encountered problem, but also relatively easy to solve. When it really can't be solved by process means, it can be improved by considering the mold design and manufacture, which is generally solvable.
Tips: when this kind of problem occurs, we should observe the movement stroke of the screw of the injection molding machine while injection molding. Particular attention should be paid to the completion of the holding pressure and melt the completion of the screw's position.
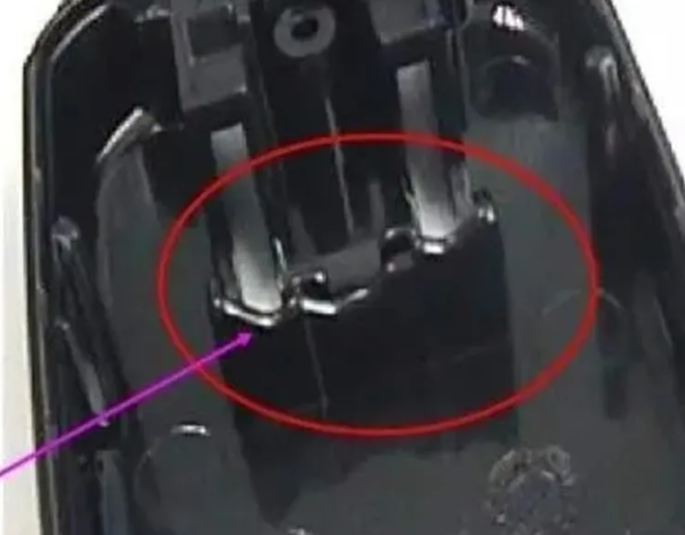
The first situation:
The injection molding machine screw melting position to reach the set value, the injection holding pressure to complete the position of 0 (the amount of residual glue is 0). Possible causes:
The injection molding machine screw melting position to reach the set value, the injection holding pressure to complete the position of 0 (the amount of residual glue is 0). Possible causes:
1. glue leakage. This situation, first of all, should immediately check the injection molding machine gun barrel has no leakage of glue; injection molding machine injection nozzle and the mold between the main bushing with the bit whether the leakage of glue. If there is a leakage of glue, the product is not full of glue is of course the phenomenon, should be excluded first. Only in the case of confirming that there is no leakage of glue, only the following checks.
When the product is not full of glue and there is no glue leakage, the amount of glue may be insufficient. At this time, it is necessary to increase the melt stroke to increase the amount of glue. Increase the melt stroke to continue to inject while observing the screw residual amount of glue, melt stroke and the product into the glue situation.
2. Insufficient amount of glue. Increase the melt stroke, the product into the glue increase, that the amount of glue is not enough, need to continue to increase the melt stroke. When the melt stroke reaches the maximum, the product is still not glue, you need to replace the large size of the injection molding machine.
3. over the glue mediator leakage. Such as with the increase of the melt stroke, injection molding products into the amount of glue and not a corresponding increase, it may be the injection molding machine over the glue medium leakage.
Check the overgluing meson leakage method: retain a certain injection cycle of the product in the mold cavity, switch to manual injection of glue. Injection pressure from small to large, observe the screw's forward amount can be judged over the glue media leakage. Manual injection of glue, the screw does not advance, indicating that the overglued media sealing is good, no leakage. In the larger injection pressure, the screw has a small amount of forward, is allowed, this time is not a leakage of the melt, but the melt is pressurized by what kind of contraction.
Where the product is not full of glue, first of all, we must check the injection molding machine barrel, injection molding machine injection nozzle molds between the occurrence of no leakage of glue; second is to check the injection molding machine screw at the front end of the overglue meson with or without leakage of glue. Only after the exclusion of these two cases, in order to carry out other aspects of the judgment, the following determination method, are established in the exclusion of these two cases, will not be repeated.
The second situation:
The screw of the injection molding machine can reach the set stroke of the melt, but cannot reach the set stroke of the injection (there is a residual amount of glue). This situation means: there is molten rubber in the barrel, but it cannot be injected into the mold cavity. Possible causes:
The screw of the injection molding machine can reach the set stroke of the melt, but cannot reach the set stroke of the injection (there is a residual amount of glue). This situation means: there is molten rubber in the barrel, but it cannot be injected into the mold cavity. Possible causes:
1. the liquidity of the melt is not enough.
The fluidity of the melt is not enough, the flow resistance is large, the gel is difficult to fill the mold. This situation may be caused by the following reasons:
a) Poor fluidity of the raw material itself;
b) The processing temperature of the gun barrel is set too low or the temperature does not reach the set value, e.g. the temperature display is not true.
c) low mold temperature, although the colloid fluidity in the barrel of the gun is good, but after flowing into the mold runners, the cooling is too fast, in the mold runners in the cavity of the poor fluidity, resulting in the filling of glue is not full.
2. improperly set injection molding process parameters.
Injection pressure is low, the gel can not overcome the resistance to glue filling; injection speed is low, long cooling time when filling the melt, liquidity is reduced, resulting in a large resistance to glue filling; injection holding time is short, the product is not full before stop filling, etc., will lead to the product is not full of glue.
3. Glue filling channel blockage.
Due to cold glue, impurities or other substances blocking the glue filling channel and lead to filling but not glue, will also lead to the product is not full of glue. At this time you need to check the injection molding machine nozzle, the main flow channel, manifolds, sprues, etc. is smooth, if there is a blockage needs to be cleaned up.
4. mold pouring system defects.
Mold casting system defects are divided into the following aspects:
a) the runner is too small, too thin or too long, increasing the fluid resistance;
b) The runner and gate are rough with scars, or have sharp angles and poor surface roughness, which affects the material flow;
c) Cold material wells are improperly set or not set, cold glue collection is incomplete, resulting in blockage of runners or sprues;
d) improperly set the location or number of sprues, filling resistance is greater than the injection pressure, the gel can not be filled into the mold;
e) poor mold exhaust or exhaust location is not properly set up, the mold local air trapped resulting in product filling is not full.
e) poor mold exhaust or exhaust location is not properly set up, the mold local air trapped resulting in product filling is not full.
5. Bad product design.
Poor product structure design, uneven design of the gel position, local gel position is too thin, resulting in product filling is not full.
If you have mold customization needs,please contact us!
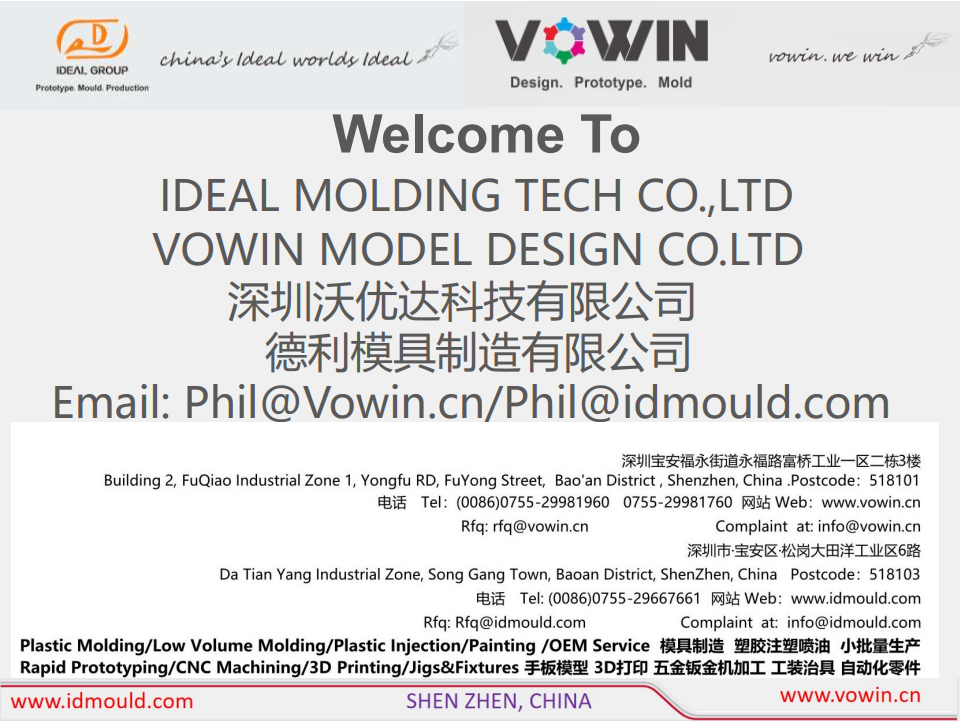
Posts by Topic
Recent Posts
- What do we need to pay attention to the plastic mold machining process and machining procedures?
- What kinds of plastic mold materials?
- What is the process of mold manufacturing?
- What should be paid attention to the polishing of injection molds?
- What is easy to ignore when maintaining and overhauling injection molds?
- What are the 6 systems of plastic molds?
- What are the methods of strengthening the surface of injection molds?
- What are the methods of insulation for injection molds?
- How to solve the problem of injection mold release difficulty?
- How can we increase the brightness of ABS injection molded parts?