Injection molds compared with other molds, the structure is more complex and precise, the operation and maintenance of the product requirements are also higher, so in the entire production process, the use of positive solutions and careful maintenance, maintenance to maintain normal production, improve efficiency, has a very important significance.
First, select the appropriate molding equipment, to determine the reasonable process conditions, if the injection molding machine is too small to meet the requirements, too large and a waste of energy, and will be due to the clamping force adjustment is not appropriate and damage to the mold or template, but also to reduce efficiency.
Selection of injection machine, should be based on the maximum injection volume, the effective distance from the tie rod, the template on the mold mounting size, the maximum mold thickness, minimum mold thickness, template stroke, ejector mode, ejector stroke, injection pressure, clamping force and other items to verify that the requirements are sufficient to be used only after the requirements. Reasonable determination of process conditions is also one of the contents of the correct use of the mold, clamping force is too large, the injection pressure is too high, the rate of injection is too fast, the mold temperature is too high will cause damage to the service life of the mold.
Second, after the mold is installed on the injection molding machine, the first empty mold running. Observe the operation of its parts of the action is flexible, whether there are abnormal phenomena, ejector stroke, open the stroke is in place, close the mold section of the surface is a close match, whether the pressure plate screws are tightened and so on.
Third, the use of molds, to maintain a normal temperature, in the normal temperature work, can extend the service life of the mold.
Fourth, the sliding parts of the mold, such as guide pillar, back to the needle, push rod, core, etc., to be observed at all times, regular inspection, timely scrubbing and filling lubricating grease, especially in the summer when the temperature is high, at least two times per shift to ensure that the sliding parts of the movement of the flexibility to prevent the tightness of the bite.
Fifth, each time before locking the mold, should pay attention to, the cavity is clean, absolutely not allowed to leave residual products, or any other foreign matter, clean up is strictly prohibited the use of hard tools, in order to prevent bruising the cavity surface.
Sixth, the cavity surface has special requirements of the mold, the surface roughness Ra less than or equal to 0.2cm, absolutely can not be wiped by hand or cotton wool wipe, compressed air should be blown, or with a high-grade napkins and high-grade degreasing cotton dipped in alcohol gently wiped.
Seventh, the cavity surface should be regularly cleaned, injection molds in the molding process will often decompose low molecular compounds corrosion mold cavity, making the shiny cavity surface gradually become dull and reduce product quality, so the need for regular scrubbing, scrubbing can use alcohol or ketone agents scrubbing should be blown dry in a timely manner.
Eighth, operation away from the need for temporary shutdown, the mold should be closed, do not let the cavity and core exposed to prevent accidental damage, downtime is expected to be more than 24 hours, the cavity, the core surface sprayed with rust oil or mold release agent, especially in humid areas and the rainy season, even if it is a short period of time should be done to prevent rust treatment.
Water vapor in the air will reduce the surface quality of the mold cavity and the surface quality of the products. Molds used again, the mold should be removed from the oil, wipe clean before use, there are mirror requirements for cleaning compressed air blow-dry and then blow-dry with hot air, otherwise it will ooze out of the molding and make products defective.
Ninth, after a temporary shutdown boot, open the mold should check whether the slider limit is moving, no abnormalities found before closing the mold. In short, before starting the machine must be careful, not careless.
Tenth, in order to extend the service life of the cooling waterway, when the mold is out of service, should immediately use compressed air to remove the water in the cooling waterway, with a small amount of oil into the mouth of the mouth, and then blowing with compressed air, so that all the cooling pipes have a layer of rust-resistant oil layer.
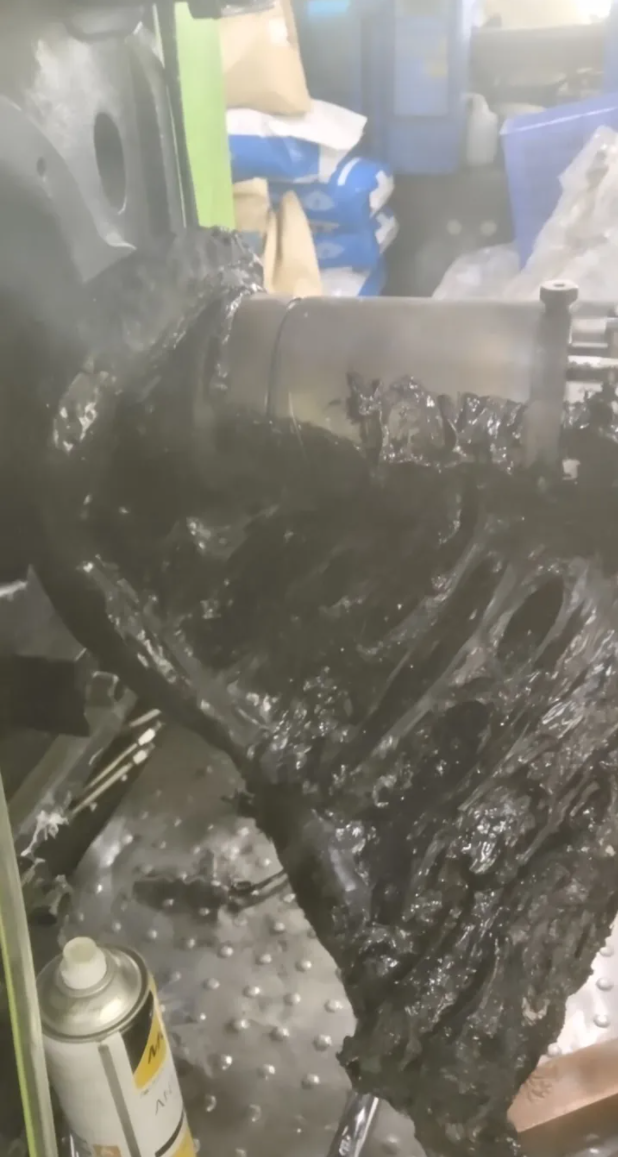
Eleventh, work carefully check the working status of the control components, to prevent abnormalities in the auxiliary system, heating, control system maintenance of the hot runner mold is particularly important. At the end of each production cycle, should be stick heaters, band heaters, thermocouples learn to measure with the European mother, and compared with the mold's technical description of the information to ensure that its function is intact. At the same time, the control circuit may be tested by means of an ammeter installed in the circuit. Core extraction with the hydraulic cylinder in the oil as much as possible to empty, the oil nozzle sealed, so as not to leak hydraulic oil in the storage and transportation process or contamination of the surrounding environment.
Twelfth, in the production of the mold heard a strange sound or other abnormalities, should immediately stop the machine to check. Mold maintenance personnel on the normal operation of the mold in the workshop to carry out inspections, found that there are abnormalities, should be dealt with in a timely manner.
Thirteenth, the operator in the shift handover, in addition to the handover of production, process critical records, the use of mold conditions should also have a detailed account.
Fourteenth, when the mold to complete the number of products produced, to replace other molds off the machine, the mold cavity should be coated with rust inhibitor, the mold and its accessories sent to the mold maintenance staff, and attached to the last mold production of qualified products as a sample sent to the maintenance staff. In addition, should also be sent to a list of mold use, fill in the details of the mold on what machine, from a certain year, a certain month, a certain date, a total of how many products are produced, whether the mold is now good. If there is a problem with the mold, to fill in the use of the list of what problems exist in the mold, put forward specific requirements for modification and improvement, and hand over a sample of unprocessed mold to the custodian, left to the mold workers to repair the mold for reference.
Fifteenth, should set up a mold library, set up a person to manage, and the establishment of mold files, if possible, to implement computer management of mold. Mold library should choose a small moisture ventilation place, the temperature should be kept below 70%, if the humidity exceeds 70%, the mold is easy to rust, mold should be stored on the shelf, pay attention to corrosion, dust and so on. To mark the need for repair or completion of repair, maintenance of the logo.
If you have mold customization needs,please contact us!