Resources
Advantages and disadvantages of injection molding vs blow molding
Release time:2023-09-22
Injection molding VS Blow molding
Injection molding process and blow molding process are also plastic plastic production process, a closer look will find that the two have obvious differences in the principle of each has its own advantages, Ideal mould is here to introduce you to the injection molding process and blow molding process advantages and disadvantages of the difference are what.
Injection molding is the type of blank in the injection mold to complete, blow molding is the type of embryo in the blow mold to complete. Generally, blow molded products are hollow, injection molding because there is an injection port, so the molded product will be more than a small piece of unwanted parts will be cut off.
1. Injection molding process
Advantages: the wall thickness distribution of the injection mold can be accurately controlled by the injection mold, thus making the wall thickness of the container is more uniform, avoiding the thinning phenomenon that is likely to occur in the corner part of the general blow molded products. All the blanks made by injection can be blown into the blow mold, which reduces the waste of molding materials and saves the trimming time of the products.
Disadvantages: injection molding products must use injection and blow molding two sets of molds and a hollow core mold with logging, and the cost of injection molds and core molds are relatively high; injection of the parison temperature is high, high-temperature parison in the injection mold after blowing need longer cooling time, so that the product of the entire molding cycle to extend the production efficiency is reduced; injection of the parison of the internal stress is greater, coupled with the conversion of molds are susceptible to uneven cooling In addition, when changing molds, it is easy to be unevenly cooled, thus increasing the risk of stress cracking of polyolefin plastic blow molded containers. Each product must use two pairs of molds, injection blank mold and blow molding mold. Injection blank mold to be able to withstand high pressure, two pairs of mold positioning tolerance level is higher, the mold cost increases, the shape and size of the production container is limited, not suitable for the production of containers with handles.
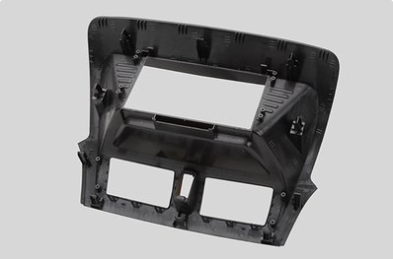
2. Blow molding process
Advantages: blow molding machinery, especially the lower cost of blow molds, molding similar products, the cost of blow molding machinery is about 1/3-1/2 of the cost of injection machinery, the production cost of products is also lower. Blow molding, the parison is in the lower pressure through the head molding and in the low-pressure, most of the 0.2-1.0mpa under the blowing, so the residual stress of the product is smaller, resistance to tensile, impact, bending and environmental strains such as the performance of the higher, with a better use of performance. And in injection molding, the melt to be under high pressure 15-140mpa through the mold runners and gates, which will lead to uneven stress distribution. The relative molecular mass of blow molding grade plastics, such as pe, is much higher than that of injection grade plastics. The wall thickness of the product is uniform, no need to carry out post-trimming process, the product has no seam line, and less waste material.
Disadvantages: the design requirements of the blow mold, should be equipped with exhaust grooves, the bottom of the design concave, mold body selection of corrosion-resistant carbon tool steel and ordinary alloy steel. Pipe billet temperature and blow molding temperature. Temperature is too high melt viscosity is low and easy to deform, so that the billet in the transfer of uneven thickness. Temperature is too low products often with more internal stress, easy to use deformation and stress rupture.
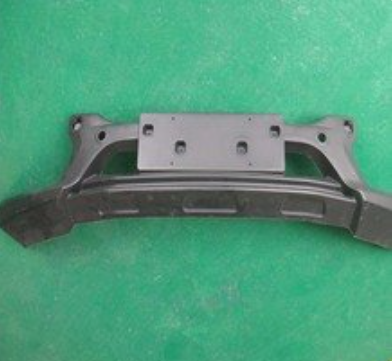
3. The injection molding process and blow molding process comparison
At present, injection molding is applicable to almost all thermoplastics, and over the years, injection molding has also been successfully used to mold certain thermosetting plastics. The molding cycle of injection molding is short, the quality of molded products can be from a few grams to dozens of kilograms, and can be formed in a single molding of complex shapes, precise dimensions, with metal or non-metallic inserts of the molded products. The adaptability of the method is strong, high production efficiency.
Blow molding is more widely used, by gas pressure to make the closed in the mold of the hot billet blown into a hollow product, or pipe billet moldless blowing into a tube film a method. This method is mainly used for the manufacture of various packaging containers and tubular films. As long as the melt index of 0.04 ~ 1.12 are better hollow blow molding materials, such as polyethylene, polyvinyl chloride, polypropylene, polystyrene, thermoplastic polyester, polycarbonate, polyamide, cellulose acetate and polyacetal resin, etc., of which polyethylene has been applied to more.
If you have project needs, please contact us!
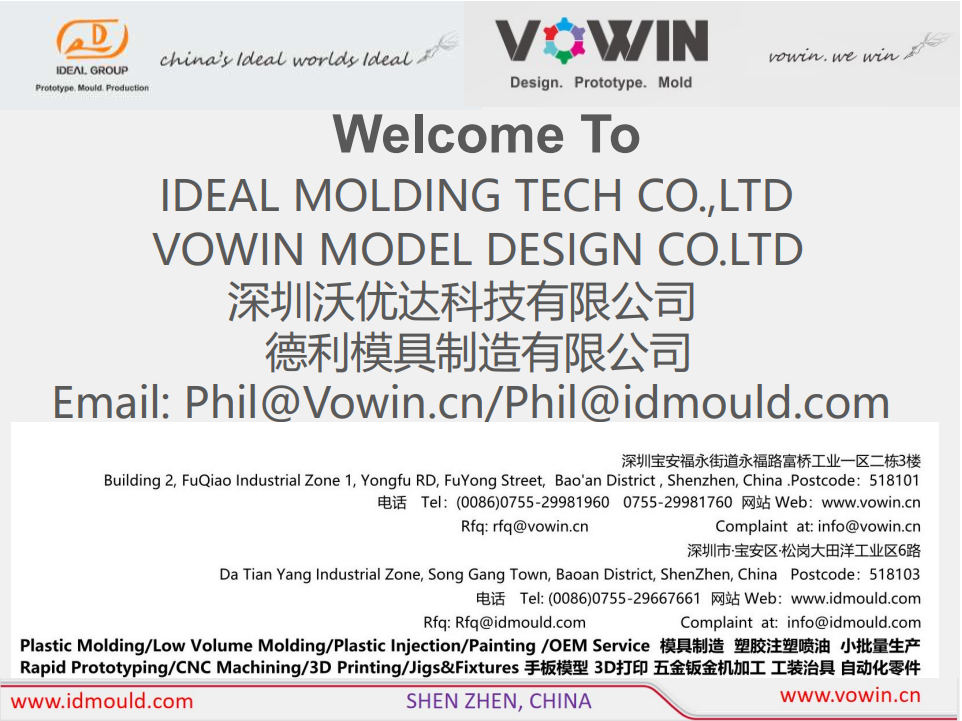
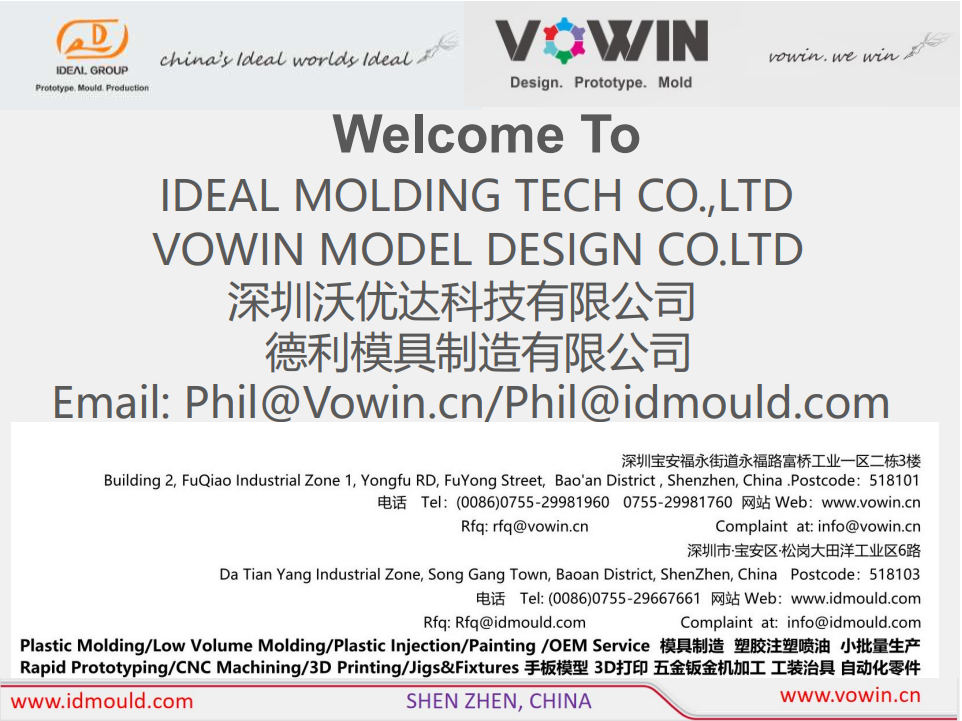
Posts by Topic
Recent Posts
- What affects injection mold machining accuracy and productivity?
- Shenzhen top five mold manufacturers: how plastic products are processed and produced?
- Shenzhen Ideal Vowin mold manufacturer: how to effectively improve the precision of mold processing?
- Chrome plating, a process that makes cars stylish
- Six injection molding processing technologies for home appliance plastic products
- Advantages and disadvantages of injection molding vs blow molding
- What is automotive hot stamping and molding technology?
- What is the difference between a hot runner and a cold runner in the mold?
- Automotive stamping die in large, precision and other areas of progress is obvious, the rapid development of plastic and rubber molds
- The top ten problems that are likely to occur in the mold testing process