Resources
Dynamic cavity temperature control requires no water
A joint project between three German injection molding companies has created a temperature control system in which CO2 replaces H20, according to supplier gwk. Brand-new perspectives and possibilities are offered by dynamic temperature control using CO2. This new and environment-friendly procedure provides a solution for heating and cooling of complex and thin-walled moulded parts. By using gaseous media for heating and cooling processes, soiled cooling channels can be eliminated CO2, it’s not just for cooling systems anymore.
Basically, it is true that gaseous media have the disadvantage of being poor heat carriers. This applies at least to air, which is only used for cooling processes under special circumstances. But in contrast, if the opportunities of CO2 are properly developed and implemented, it offers an interesting
alternative to conventional water temperature control.
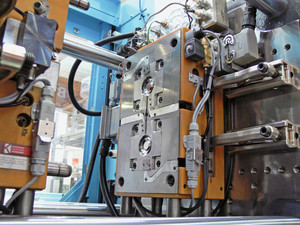
An application for injection moulding of thick-walled optical lenses made of PMMA for LED lighting employs a waterless cyclic cavity temperature control with CO2. Mould inserts that were produced by means of the company’s integrat 4D-process provide precise and quick heat transfer in the mould , which is operated with high energy efficiency on an all-electric
injection moulding machine from Sumitomo Demag.
- What affects injection mold machining accuracy and productivity?
- Shenzhen top five mold manufacturers: how plastic products are processed and produced?
- Shenzhen Ideal Vowin mold manufacturer: how to effectively improve the precision of mold processing?
- Chrome plating, a process that makes cars stylish
- Six injection molding processing technologies for home appliance plastic products
- Advantages and disadvantages of injection molding vs blow molding
- What is automotive hot stamping and molding technology?
- What is the difference between a hot runner and a cold runner in the mold?
- Automotive stamping die in large, precision and other areas of progress is obvious, the rapid development of plastic and rubber molds
- The top ten problems that are likely to occur in the mold testing process