3. After welding, the press plate and the lower surface of the mold for research and matching.
2、Cutting edge chipping
Mold in use due to various reasons caused by the chipping, will have a certain impact on the quality of the parts. It is one of the most common repairs in the mold repair, the chipping of the knife edge repair steps are as follows:
1. According to the situation of chipping, if the chipping is very small, usually the chipping place with a grinder to ensure that the welding is solid, not easy to chipping again;
2. Welding with the appropriate electrodes, we currently use the D332 electrodes to the edge of the surfacing. Surfacing must be selected before the repair of the reference surface, including the gap surface and non-gap surface;
3. Flatten the non-gap surface of the cutting edge (refer to the datum left beforehand);
4. Scribe against the transition piece, if there is no transition piece can be left beforehand with the benchmark for rough grinding gap surface;
5. On the machine to repair the gap surface, with the help of clay and other auxiliary research and matching. In the process of repair must be careful, open the press as slow as possible, if necessary, with the mold height adjustment downward open, in order to avoid the phenomenon of bad cutter nibble;
6. knife gap should be reasonable, for the steel plate stamping die, one side of the knife gap to take the thickness of the plate 1/20. but in the actual operation process, you can use the plate test punch to test the size of the gap, as long as the shear after the parts of the burr to meet the requirements can be, in general, the size of the burr is determined by the standard, the burr height is not greater than the thickness of the plate 1/10;
7. Detect whether the gap surface of the cutter and shear the direction of unity;
8. Gap with a good, with an oil stone will be the gap surface of the cutter push smooth, in order to reduce the production of sheet and cutter friction and the resistance of the waste drop.
3、Pulling hair
Knife edge chipping hair mainly occurs in stretching, molding and flanging and other processes.
Solution:
1. First of all against the parts to find out the corresponding position of the mold pulling hair;
2. Use the oil stone to push the corresponding position of the mold, pay attention to the uniform size of the rounded corners;
3. Use fine sandpaper to polish the part of the mold pushed smooth, sandpaper in 400 or more.
4、Trimming and punching with material
The main reason for trimming and punching with material is: trimming or punching the mold pressure or unloading device is abnormal.
Solution:
1. Find out the corresponding part of the mold according to the part of the workpiece;
2. Check whether there is any abnormality in the press and unloading plate of the mold;
3. Patch weld the corresponding part of the press plate;
4. Combined with the parts will be welded parts to repair smooth, the specific type of surface and process parts with the preparation;
5. Test punch;
6. If the check is not the mold pressure unloading plate problem, you can check the mold knife block whether there is hair phenomenon.
5、Waste cut continuously
For waste cut constantly phenomenon, first analyze why it cut constantly, the main reason is because the operator in the production process did not clean up the waste in a timely manner, resulting in the accumulation of waste, and finally in the upper trimming knife block under the pressure caused by the collapse of the edge of the waste knife, the repair method and trimming the collapse of the edge of the approach is similar to the repair process must pay attention to the height of the trimming knife block, not to be described in detail here. If the repair is too high, it will cause the knife block and the upper trimming knife block interference, thus causing the waste knife block again damaged; if the repair is too low, it will form the waste cut constantly phenomenon, so in the repair of the waste knife not only to take into account the gap surface of the knife block, at the same time the height of the knife block is also very important. The difficulty of its repair is greater than the difficulty of the simple edge of the knife chipping. But as long as you select a good datum before repair, you can still repair it with ease.
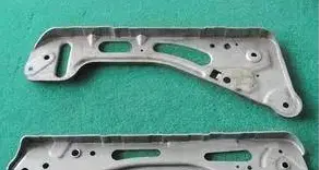
6、burr
Parts in the trimming, punching and drop easy to burr too large a phenomenon, the main reason for the burr for the mold edge gap and edge gap is small two categories:
When the gap is large: the section of the bright band is very small or basically invisible, the burr is characterized by thick and large, not easy to remove;
When the gap is small: the cross-section of the two bright bands, due to the gap is small, the burr is characterized by high and thin.
Repair method when the gap is large:
1. trimming and punching process using the convex die does not move while repairing the concave die approach, while the drop process is based on the concave die, that is, the size of the concave die remains unchanged, by repairing the convex die approach. The above difference is to ensure that the product size is not affected before and after repair;
2. Find out the part of the mold edge clearance against the production piece;
3. Use the corresponding welding rod (D332) for this part of the filler to ensure the hardness of the mold edge;
4. Repair and match the gap between the cutter (the same method as the cutter chipped edge).
Gap hours of repair methods:
1. The specific situation based on the size of the mold gap to adjust to ensure that the gap is reasonable. For trimming punching die, the gap is placed in the concave die approach, while for the drop die should be used to enlarge the convex die approach, thus ensuring that the size of the parts before and after the repair remains unchanged;
2. After the repair is completed, measure the vertical of the gap surface, and use the plate to test whether the gap reaches the reasonable requirements.
For punching die, after its burr, if the convex die or concave die wear, you can find the corresponding standard parts for replacement, if there is no standard parts, you can use patch welding or mapping for manufacturing. In addition, one point in particular, for alloy steel materials and other materials with poor welding performance, special treatment should be carried out before welding, such as: preheating, etc., otherwise it will cause cracking of the mold.
7、Punching waste clogging
Punching waste clogging is a more common type of failure in the punching mold, the reasons for this are: the waste channel is not smooth, the waste channel has an inverted taper, the waste is not cleaned up in time and so on.
Causes:
1. The mold is not smooth, the surface of the processing lines, etc.;
2. Inverted taper of the mold, resulting in the waste path on the big and small and thus waste material blockage.
Repair method:
As long as to ensure that the A side and B side are in a smooth and equal diameter state can ensure that the waste will not be blocked.
If you have mold customization needs,please contact us!