Another problem with plastics is their dryness and whether they are mixed with debris. Some plastics, such as nylon and ABS, are highly absorbent, and water can soak through the surface of the plastic and combine directly with the plastic molecules, thus affecting the performance of the plastic. As for polycarbonate, although it is not water-absorbent, its performance is also sensitive to water on its surface. Therefore, when injection molding, many plastics must be pre-dried in order to properly perform. It is of course even more difficult to predict changes in the properties of plastics if they are mixed with debris, or if they are mixed with different types of plastics.
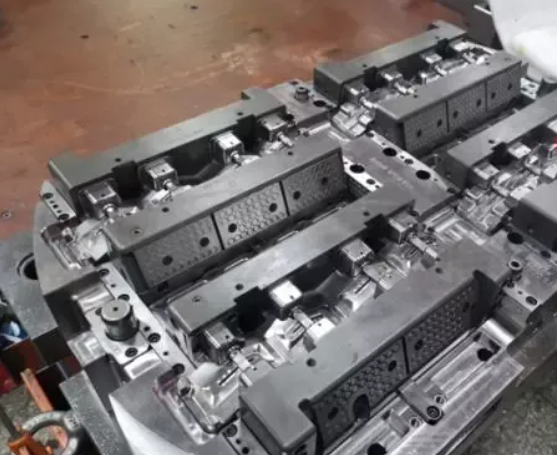
The pressure of plastic in the mold cavity will change with the filling of the mold cavity, before the mold cavity is not filled, the pressure at the front of the melt is almost zero, and the pressure at the injection port is higher than the pressure at other locations in the mold cavity. However, when the mold cavity is completely filled, the pressure loss during plastic flow no longer exists, and the pressure in the entire mold cavity becomes the same hydrostatic pressure, thus the force to open the mold will increase, resulting in the production of burrs, in order to avoid this situation, once the mold cavity is filled, the injection pressure must be adjusted to a lower holding pressure.
In addition to correctly adjusting the pressure control system of the injection machine, another auxiliary way is to reduce the injection speed first, so that the plastic at the front of the melt will have time to cool down and partially solidify, thus avoiding the production of burrs, due to the injection speed is too slow will reduce the production efficiency, the best method of adjustment of the injection speed is to be adjusted in sections, so that the average speed of the injection process will not be too slow.
Because the injection speed is too fast will increase the pressure damage, increase the average pressure of the plastic in the mold cavity, so the adjustment of the injection speed must also be used in conjunction with the clamping force, otherwise, it may also produce burrs.
If the mechanical structure of the injection molding machine has a problem, the complexity is greater, to find the cause of the problem is also more difficult, such as mold parallelism deviation, or mold tie rod force is not uniform, can also cause mold force imbalance, so that the plastic parts in the clamping force of the weaker position of the Phi Feng.
On the other hand, if the screw or the melt cylinder is worn out, the melt may slip and flow backward between the threaded O.D. and the melt cylinder, resulting in incorrect pressure switching points, causing localized burrs and insufficient injection.
In addition to the above factors, if the mold problems, will also produce burrs, such as mold used for a long time, some of the position of the wear and tear, so that easy to have the phenomenon of burrs. Even some minor problems, such as air vent obstruction can also cause the mold cavity pressure increases, and the pressure is too high, there will be burrs, in some multi-cavity molds, if the runner design is not balanced, the plastic flow will be asymmetric, in order to avoid the individual cavities of the injection of glue is not enough, some other cavities may appear burrs.
Ideal Vowin Group is an injection mould & CNC machining factory, support rapid prototyping, 3D printing, mould customization, we have recently helped our customers to complete many big projects, for more details, please visit our official website: www.idmould.com / www.vowin.cn.
If you have relevant needs,please contact us!
WhatsApp: +8617369230494
Wechat: 17369230494
E-mail: yuki@idmould.com/yuki@vowin.cn