Resources
What are the common problems of mold maintenance and how to solve them?(2)
Release time:2024-03-27
What are the common problems of mold maintenance and how to solve them?
Often experience customers say you have problems with the mold, and are said to be your mold quality problems, but never reflected on the use of the process there is no problem, the following Kexiang mold manufacturer editor-in-chief to share some of the common problems in the maintenance of the mold and the solution.
9. The bending edge is not straight and the size is not stable.
① Increase the press line or pre-bending process
② Material compression force is not enough to increase the compression force
③ Convex-concave mold corner wear asymmetric or uneven bending force, adjust the gap between the convex-concave mold to make it uniform, polishing convex-concave mold corner
④ The height of the size can not be smaller than the minimum limit size
10. Bending surface extrusion material thinning
① Concave die angle is too small, increase the radius of concave die angle.
② Convex-concave die clearance is too small, amend the convex-concave die clearance
11. Uneven bottom of concave part
① Material itself is not flat, need to level the material
② Top plate and material contact area is small or not enough top force, need to adjust the top device, increase the top force
③ There is no ejector device in the concave mold, the ejector device should be increased or corrected.
④ Add shaping process
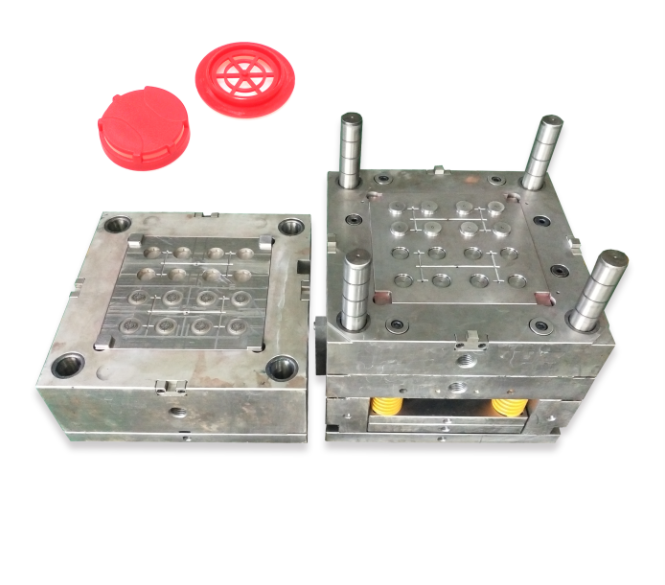
12. Stainless steel flanging deformation
Apply a good quality forming lubricant to the material before making the flanging, this will enable the material to separate better from the mold and move smoothly on the lower mold surface during forming. This gives the material a better chance to distribute the stresses caused by bending and stretching, preventing deformation on the edges of the formed flanges and wear on the bottom of the flanges.
13. Material distortion
Punching a large number of holes in a material results in poor material flatness, which can be caused by the accumulation of punching stresses. When punching a hole, the material around the hole is stretched downward, increasing the tensile stress on the upper surface of the plate, and the downward punching motion also causes an increase in the compressive stress on the lower surface of the plate. For punching a small number of holes, the result is not significant, but as the number of holes increases, the tensile and compressive stresses increase exponentially until the material is deformed.
One way to eliminate this deformation is to punch every other hole and then return to punching the remaining holes. This produces the same stresses in the sheet, but dismantles the tensile/compressive stress buildup that occurs when holes are punched one after another in the same direction. This also causes the first batch of holes to share the deformation effect of the second batch.
14. Severe wear of the mold
① Timely replacement of worn mold guide components and punches.
② Check whether the mold clearance is unreasonable (small), increase the lower die clearance.
③ Minimize wear and tear, improve lubrication conditions, lubricate the plate and punch. The amount of oil and the frequency of oil injection depends on the conditions of the processed material. Cold-rolled steel, corrosion-resistant steel and other materials without rust and scale, to the mold oil injection, oil injection points for the guide sleeve, oil injection port, the lower die and so on. Use light machine oil for the oil. Materials with rust and scale, when processing rust micro-powder will be inhaled between the punch and the guide sleeve, resulting in dirt, so that the punch can not slide freely in the guide sleeve, in this case, if the oil, it will make the rust and scale more likely to be stained, so when punching this material, on the contrary, the oil should be wiped clean, decomposed once a month, with gasoline or diesel fuel to the punch, the lower die of the dirt, and then wiped clean before reassembling. This will ensure that the mold has good lubricating properties.
④ Improper sharpening methods, resulting in annealing of the mold, aggravating wear, should use soft abrasive grinding wheels, using a small amount of draft, a sufficient amount of coolant and often clean up the grinding wheel.
15. Prevent stamping noise
Punching machine is the necessary equipment for plate processing industry. Punching machine in the work will produce mechanical transmission noise, stamping noise and aerodynamic noise, the high value of the noise can be up to 125dB (A) greatly exceeds the national standard of 85dB (A) and the following noise index requirements, and thus the operation of the workers and the surrounding environment (such as offices, residential areas, meeting rooms, etc.) caused extremely serious harm and pollution, effective management of the noise has become an urgent problem. Effective control of the noise has become an urgent problem. Starting from the punch press noise source and mold structure, to reduce the noise need to pay attention to the following points.
① Focus on mold maintenance, clean, keep the edge sharp.
② Mold edge shape, number, material and punching line length, mold edge and parts contact surface is not too large, punch to do oblique edge step punching, so that the mold in different positions into the depth of different, the whole process to achieve the real cut off, rather than synchronized extrusion.
③ The edge of the mold must be perpendicular to the installation surface, and the edge of the convex-concave die with reasonable clearance, unloading difficulties can increase the lower die clearance, increase the unloading force, the use of soft-surface unloading plate and other methods.
④ The matching precision between the working templates, processing some exhaust grooves.
⑤ Change the stop plate to small pieces, and change the discharging plate and lower template to insert type to reduce the slamming area.
⑥ Stripper plate spring top source changed to T-type top rod, spring mounted on the upper mold seat, isometric sleeve and top rod with, open mold state to ensure that the stripper plate still have a certain amount of free movement.
⑦ Maintain good lubrication, mold non-interference, smooth.
⑧ Upper and lower die seat surface pad aluminum plate to do impulse buffer.
⑨ Mold debugging is good, in the punch with sound insulation cover or sponge board sound insulation processing, ⑩, improve the accuracy of the punch press, the
⑩ To improve the accuracy of the press, reduce structural noise. Installation of cushioning and noise reduction cylinders on the bench, gears using helical gear to strengthen lubrication and gear cover, pneumatic system with muffler.
Ideal Vowin Group is an injection mould & CNC machining factory, support rapid prototyping, 3D printing, mould customization, we have recently helped our customers to complete many big projects, for more details, please visit our official website: www.idmould.com / www.vowin.cn.
If you have relevant needs,please contact us!
WhatsApp: +8617369230494
Wechat: 17369230494
E-mail: yuki@idmould.com/yuki@vowin.cn
Posts by Topic
Recent Posts
- What do we need to pay attention to the plastic mold machining process and machining procedures?
- What kinds of plastic mold materials?
- What is the process of mold manufacturing?
- What should be paid attention to the polishing of injection molds?
- What is easy to ignore when maintaining and overhauling injection molds?
- What are the 6 systems of plastic molds?
- What are the methods of strengthening the surface of injection molds?
- What are the methods of insulation for injection molds?
- How to solve the problem of injection mold release difficulty?
- How can we increase the brightness of ABS injection molded parts?