Resources
What are the methods of product surface process treatment?
Release time:2023-11-23
What are the methods of product surface process treatment?
First, the surface of three-dimensional printing (water transfer printing)
Water transfer printing is the use of water pressure and activator to make the water transfer carrier film on the peeling layer dissolved transfer, the basic process for:
1, the printing of the film: in the polymer film printed on a variety of different patterns.
2, spray primer: many materials must be coated with a layer of adhesive, such as metal, ceramics, etc., if you want to transfer a different pattern, you must use a different base color, such as wood grain basic use of brown, brown, earthy yellow, etc., the basic use of stone pattern white, etc.
3, the film extension: let the film on the water surface flat, and to be the film stretching flat.
4, activation: special solvents (activator) to make the pattern of the transfer film activated into the state of ink.
5, transfer: the use of water pressure will be activated by the pattern printed on the printed material;
6, washing: the impurities left in the printed workpiece will be washed with water.
7, drying: will be printed workpiece drying, the temperature depends on the material of the vegetal and melting point of the depending.
8, spray top coat: spray transparent protective lacquer to protect the surface of the printed object.
9, drying: dry the surface of the object after spraying the top coat.
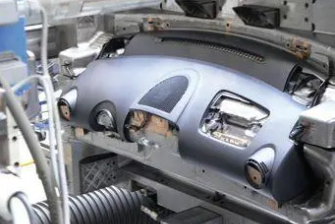
There are two types of water transfer technology, one is the water labeling transfer technology, the other is the water phi transfer technology, the former is mainly to complete the transfer of text and portrait patterns, the latter tends to be in the entire product surface for complete transfer.
Cubic transfer technology (Cubic Transfer) uses a water-based film that is easily dissolved in water to carry graphics. Due to the excellent tension of the water-based film, it easily wraps around the surface of the product to form a graphic layer, and the surface of the product is painted to give it a completely different appearance. Lamination transfer technology can be used to apply color graphics to any shape of workpiece, solving the problem of three-dimensional product printing for manufacturers.
Curved surface lamination can also add different textures to the surface of the product, such as leather, wood, jade and marble, etc. It can also avoid the false position that often occurs in general panel printing. During the printing process, there is no need for the product surface to come into contact with the printing film, thus avoiding damage to the product surface and its integrity.
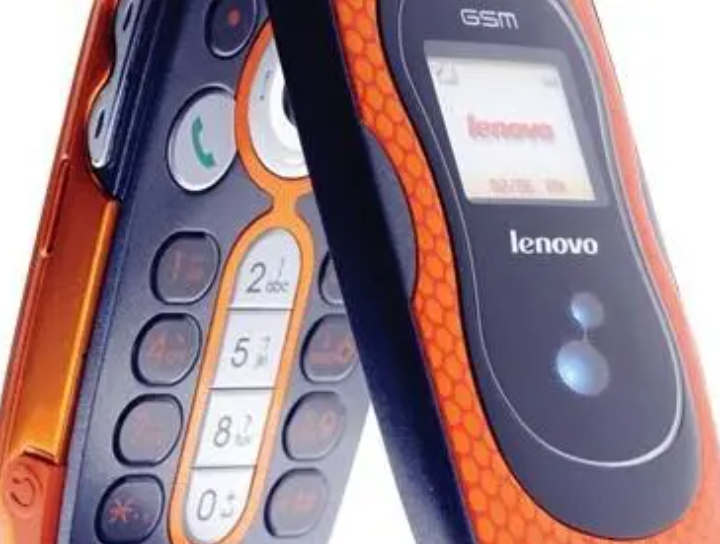
Second, metal drawing (Bench drawing metal)
Aluminum alloy surface drawing process: drawing can be made according to the needs of decoration, straight, chaotic, threaded, corrugated and spinning and other kinds of threads.
1, Straight wire drawing refers to the surface of aluminum plate with mechanical friction method to process a straight line pattern. It has the dual role of brushing off scratches on the surface of aluminum and decorating the surface of aluminum. Straight wire drawing has two kinds of continuous filigree and intermittent filigree.
Continuous filigree can be used by cleaning cloth or stainless steel brush through the surface of the aluminum plate for continuous horizontal straight line friction (such as in the conditions of the device underhand technical grinding or planer clamped steel wire brush in the aluminum plate grinding brush) to obtain. By varying the wire diameter of the stainless steel brushes, different thicknesses of grain can be obtained. Intermittent wire grain is generally processed in the brushing machine or rubbing machine to produce.
Preparation principle: the use of two groups of co-rotating differential wheel, the upper group of fast-rotating grinding rollers, the lower group of slow rotation of the rubber rollers, aluminum or aluminum alloy plate from the two groups of rollers through, was brushed out of the delicate intermittent straight lines. 2.
2, The messy wire drawing is a kind of irregular, non-obvious pattern of matte silk grain obtained by moving the aluminum plate back and forth and rubbing it under the high-speed running copper wire brush. This kind of processing, the aluminum or aluminum alloy plate surface requirements are high.
3, Corrugation is generally made on the brushing machine or rubbing machine. Using the axial movement of the upper group of grinding rollers, grinding and brushing on the surface of aluminum or aluminum alloy plate, resulting in a wave pattern.
4, spinning pattern, also known as spinning light, is the use of cylindrical felt or research stone nylon wheel mounted on the drill press, with kerosene and polishing ointment, the surface of the aluminum or aluminum alloy plate rotating polishing obtained by a kind of filigree. It is mostly used for the decorative finishing of round signs and small decorative dials.
5, Threading is a small motor equipped with a round felt on the shaft, which is fixed on the tabletop at an angle of about 60 degrees from the edge of the table, and in addition to make a drag plate equipped with a fixed aluminum plate pressure tea, and paste a polyester film with straight edges on the drag plate to limit the degree of competition of the thread. The use of felt rotation and drag the straight line of the movement of the board, in the surface of the aluminum plate spinning friction consistent width of the thread pattern.
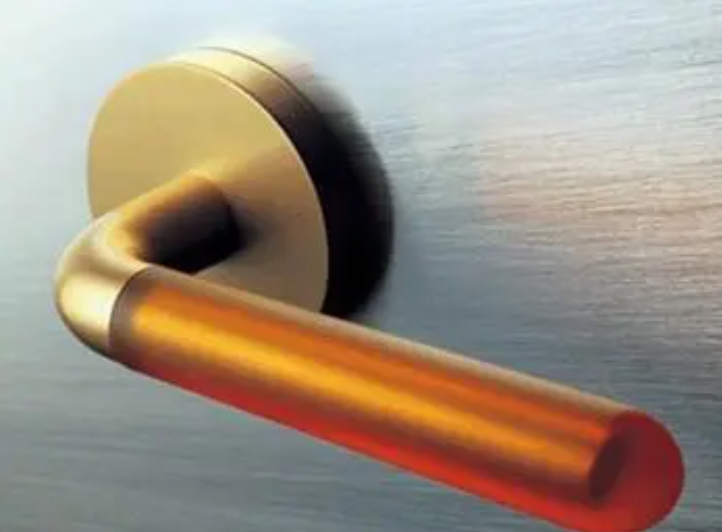
Thrid, andiozing
As a light metal, aluminum and its alloys have become more and more common in industrial design: MP3 players, DSCs, mobile phones, NBs, and even desktop computers can be seen as light metals (magnesium alloy and aluminum alloy are the mainstream), and the proportion of magnesium alloy used in NBs (including internal and external components) has even exceeded 50%, while Apple's MP3 players, desktop computers, and Sony's DSCs even use a large amount of aluminum alloy materials. Apple's MP3 players, desktop computers, and Sony's DSCs even use aluminum alloys in large quantities. Oxidation coloring of aluminum alloy is a surface treatment process commonly used for small electromechanical products, which mainly enhances the corrosion resistance of the product surface (e.g., blackening, bluing) and makes the product have a decorative effect (e.g., uniform and consistent colors).
Oxidation coloring effect is related to the material composition and process parameters of aluminum alloy. Aluminum alloy surface oxidation coloring is usually followed by subsequent treatment processes, so that the entire product is more aesthetically pleasing. Another point is that coloring is not a post-treatment of oxidation, but is carried out at the same time of oxidation.
Commonly used are the following kinds of oxidation coloring treatment methods:
1, coloring anodic oxide film aluminum anodic oxide film, relying on adsorption of dyes and coloring.
2, spontaneous color anodic oxidation film this anodic oxidation film is a particular aluminum in some kind of suitable electrolyte (usually organic acid-based) in the electrolytic effect, by the alloy itself to generate a spontaneous anodic oxidation film with color.
3, electrolytic coloring anodic oxide film coloring, coloring through the voids of the oxide film by metal or metal oxide electrodeposition.
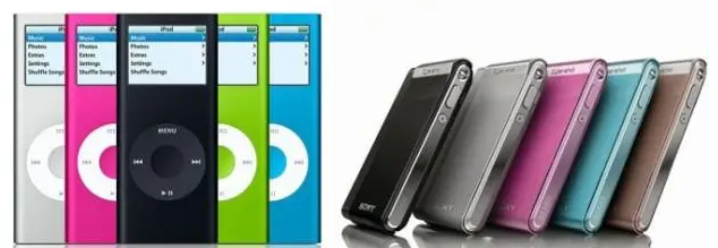
Fourth,Aluminum diamond engraving
Aluminum diamond engraving: at low temperatures can also maintain good compressive strength high hardness, high mechanical strength, good resistance to abrasion, specific gravity light relative heat index up to 80c at high temperatures can also maintain good dimensional stability fire prevention, simple process gloss, easy to color, compared to other thermoplastics lower cost Typical uses consumer electronics, toys, environmental protection goods, automotive dashboards, door panels, outdoor fencing. Typical uses Consumer electronics, toys, environmental goods, automotive dashboards, door panels, outdoor fencing.
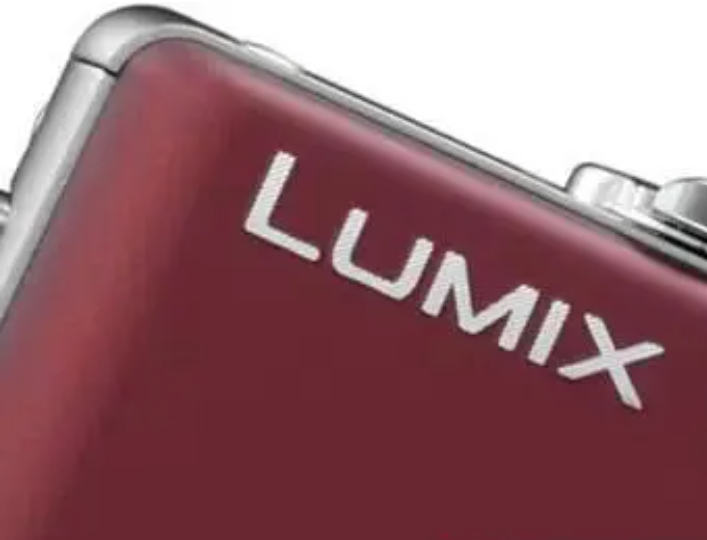
Fifth, Plating process
Electroplating process: Electroplating refers to a surface processing method in which the salt solution containing the metal to be plated is used as the cathode of the plated base metal, and the cations of the metal to be plated in the plating solution are deposited on the surface of the base metal to form a plated layer through electrolysis. The properties of the plating are different from those of the base metal and have new characteristics. According to the function of the plating layer, it is divided into protective plating, decorative plating and other functional plating.
Plating process: generally includes three stages: pre-treatment before plating, plating and post-treatment. Requirements for plating layer:
1, plating and base metal, plating and plating, there should be a good combination between.
2, the plating layer should be crystallized carefully, flat, uniform thickness.
3, the plating layer should have the required thickness and as few pores as possible.
4, the coating should have the specified indicators, such as brightness, hardness, electrical conductivity.

Sixth, NIckle electroplating
Nickel is a silver-white yellowish metal, ferromagnetic, density 8.9/g.cm-2, melting point of 14530 C. Nickel metal is soluble in dilute nitric acid, insoluble in hydrochloric acid and sulfuric acid, in nitric acid in a passivated state. Nickel and oxygen in the air, the surface quickly generate a very thin passivation film, can resist the atmosphere, alkali and some acid corrosion. Nickel and strong bases do not play a role.
The standard electrode potential of nickel is -0.25V, nickel plating has a wide range of applications, can be divided into protective decorative and functional aspects. The radiator in the following picture (appearance of the color black or black with yellow)

Seventh, Chromium electroplating
Chromium is a kind of silver-white metal with sky blue color. Although the electrode potential is very negative, but it has a strong passivation properties, the atmosphere is quickly passivated, showing the nature of the precious metal, so the iron parts of the chromium plating layer is cathodic plating. Chromium layer in the atmosphere is very stable, can maintain its luster for a long time, in alkali, nitric acid, sulfide, carbonate and organic acids and other corrosive media is very stable, but can be dissolved in hydrochloric acid and other hydrohalic acid and hot concentrated sulfuric acid.
Chromium layer of high hardness, good wear resistance, reflective ability, good heat resistance. There is no significant change in luster and hardness below 500OC; the temperature is greater than 500OC to start oxidizing and discoloring; greater than 700OC to start softening. Due to the excellent performance of chromium plating layer, it is widely used as the outer surface layer of protective and decorative plating system and functional plating layer.
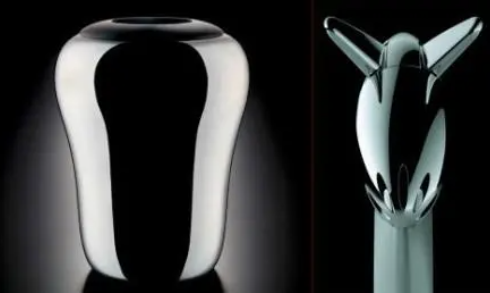
Other plating
Copper plating: copper plating layer is pink, soft, with good ductility, electrical conductivity and thermal conductivity, easy to polish, the appropriate chemical treatment can be bronze, copper green, black and this color and other decorative colors. Copper plating is easy to lose luster in the air, and carbon trioxide or chloride, the surface of a layer of alkaline copper carbonate or copper chloride film layer, by the role of sulfide will generate brown or black copper sulfide, therefore, as a decorative copper-plated layer needs to be coated with an organic cover layer on the surface.
Cadmium plating: Cadmium is a silver-white glossy soft metal, its hardness is harder than tin, softer than zinc, good plasticity, easy to forge and rolling. Cadmium's chemical properties are similar to zinc, but does not dissolve in alkali, dissolved in nitric acid and ammonium nitrate, in dilute sulfuric acid and dilute hydrochloric acid dissolved very slowly.
Cadmium vapor and soluble cadmium salts are toxic, cadmium pollution must be strictly prevented. Because cadmium pollution is very harmful and expensive, it is usually galvanized or alloy plating to replace cadmium plating. At present, the domestic production of cadmium plating solution used in more types: ammonia carboxyl complex cadmium plating, acid sulfate cadmium plating and cyanide cadmium plating. In addition, there are pyrophosphate cadmium plating, alkaline triethanolamine cadmium plating and HEDP cadmium plating.
Tin plating: tin has a silver-white appearance, atomic weight of 118.7, density of 7.3g/cm3, melting point of 2320C, the atomic price for the divalent and quaternary, so the electrochemical equivalent of 2.12g / A.h and 1.107g / A.h. Tin has corrosion-resistant, non-toxic, easy to iron weld, soft and ductile and other advantages.
Tin plating has the following characteristics and uses:
1, high chemical stability.
2, in the electrochemical sequence of tin's standard potential error iron positive, for steel is cathodic plating, only in the plating without porosity can effectively protect the substrate; 3, tin conductivity is good, easy to iron welding, soft, ductile and so on.
3, tin conductivity is good, easy to weld.
4, tin from -130C from the beginning of crystallization began to mutate, to -300C will be completely transformed into a crystalline isomer, commonly known as the "tin plague", at this time has completely lost the nature of tin.
5, tin with zinc, cadmium plating, as in high temperature, moisture and closed conditions can grow into whiskers, known as long hairs
6, tin plating in the hot oil above 2320C re-soluble treatment, you can get a glossy patterned tin layer, can be used as a decorative plating of daily necessities.
Electroplating single-metal plating and lead plating, iron plating, silver plating, gold plating and so on. Plating alloys: electroplating copper-based alloys, electroplating zinc-based alloys, electroplating cadmium-based, indium-based alloys, electroplating lead-based, tin-based alloys, electroplating nickel-based, cobalt-based alloys, electroplating palladium-nickel alloys. Composite plating: nickel-based composite plating, zinc-based composite plating, silver-based composite plating, diamond inlay composite plating.
Eighth, surface coating (plastic parts) Spary
Composition of the four major elements of the coating include:
1, resin (Resin).
2, pigment (Pigment).
3, solvent (Solvent).
4, other additives (Additive).
The types of paint drying are as follows:
1, volatile drying (the use of diluent evaporation drying).
2, fusion drying (molecules and molecules due to volatile phase-resistant polymerization).
3, oxidation drying (unsaturated fatty acids and oxygen combination in the air).
4, the use of bridging reaction and drying (the use of bridging agents, the so-called hardener to form bridges and hardening).
5, Ultraviolet hardening (unsaturated polyolipids add agent by ultraviolet wavelength 300-400mn irradiation after molecular polymerization and hardening).
UV process introduction:
UV coatings can be coated by dipping, drenching, lacquer coating, spin coating, and even vacuum coating, and then cured into a film by ultraviolet photon irradiation. Compared with general solvent-based coatings, the characteristics of UV coatings are as follows:
1, fast curing speed.
2, room temperature curing.
3, saving energy.
4, to save floor space.
5, does not pollute the environment.
6, Enhance product performance.
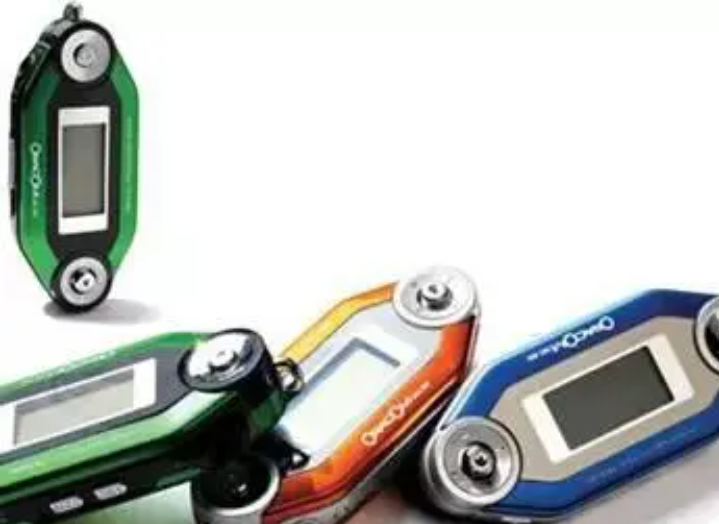
Ninth, Pad printing
Pad printing refers to - the substrate for irregular shaped surface (such as instruments, electrical parts, toys, etc.), the use of copper or steel intaglio, through the silicone rubber cast into a hemispherical pad printing head, which is pressed to the plate will be transferred to the substrate ink transfer to complete the transfer of the printing method. Pad printing process is a special printing technology introduced to China in the 80's, due to its small area, concave-convex surface of the product above the printing has a very obvious advantage, to make up for the shortcomings of the screen printing process.
In the early 1990s, with the further opening of the Chinese market, a large number of electronics, plastics, gifts, toys and other traditional industries as the main foreign-funded enterprises have entered the Chinese market, pad printing technology and screen printing technology as the main decorative way is to get extraordinary development, according to incomplete statistics, pad printing technology and screen printing technology in the above industries, the application of the above industry respectively reached 27%, 64%, 51%, 66%.
Pad printing machine applicable industries:
Plastic industry, toy industry, glass industry, metal industry, electronics industry, sporting goods, stationery industry, optical industry, IC packaging industry.
Pad printing machine applicable scope:
Rulers, pens, spherical objects, dolls eyes, watches, cameras, hair dryer shell, ceramic magnet, medical apparatus, rackets, cassette tapes, electronic parts, IC, CPU, DRAM, computer shell, keys, decorative signs, big brother chassis and other printing.
In general, the pad printing process is not high technology content, in the case of high production costs in developed countries to continue to develop is very difficult, so the pad printing industry to China, such as low labor costs in developing countries to transfer is an inevitable trend, at present, in addition to foreign countries are still manufacturing a high degree of automation of the pad printing production line of the few enterprises, most companies will move the production base to China.
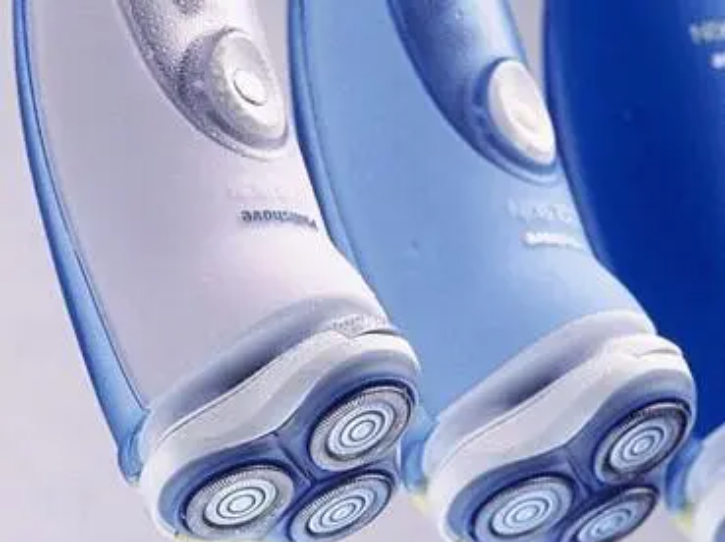
Tenth, Heat transfer print
Heat transfer is a technology that prints patterns or designs onto heat-resistant adhesive paper, and then prints the pattern of the ink layer onto the finished material by heating and pressurizing. Since the transfer operation is a single process even for multi-colored patterns, customers can shorten the pattern printing operation and reduce the loss of materials (finished products) due to printing errors. Printing with heat transfer film can create a multi-color pattern in a single pass without the need for color registration, and simple equipment can also print realistic patterns.
Thermal transfer printing equipment is used to decorate aluminum shaped materials, all kinds of metal plates, and can achieve the effect of wood products or marble. Thermal transfer equipment works according to the principle of heat sublimation, it can quickly transfer the desired wood or marble grain to the powder coated surface of aluminum shapes within 3-5 minutes and penetrate 40-60 microns into the coating.
Aluminum transfer production process:
1, Cut the roll of heat transfer film to the required size using a film machine.
2, the cut transfer film with transfer ultrasonic packaging machine according to the size of the workpiece with ultrasonic welding into the workpiece package bag.
3, Insert the workpiece into the workpiece package bag made of transfer film on the packaging platform.
4, the workpiece wrapped transfer film on the thermal transfer machine cart platform, in turn, can be put on 18 aluminum, aluminum ends connected to the vacuum pump and lock, open the vacuum switch, this time the transfer film is tightly affixed to the aluminum. The trolley automatically sends the aluminum material to the baking oven, which automatically heats up to 220 degrees and keeps the temperature for 3 minutes, and the trolley automatically exits the baking oven.
5, Loosen the vacuum pump head, remove the workpiece.
6, remove the transfer film, and check the quality of the workpiece.
The production process of lithographic thermal transfer, first, use the film cutting machine to cut the thermal transfer paper roll into the required size. Second, attach the thermal transfer paper film to the surface of the workpiece and place it on the flatbed thermal transfer printing machine. Third, push the flat plate to the heating area of the flatbed thermal transfer machine, press the switch of the platen, and the platen will press the thermal transfer paper tightly on the workpiece, heat and keep warm for one minute. Fourth, raise the platen, push the workpiece to the piece section, remove the transfer film to remove the workpiece and check.
Thermal transfer technology is widely used in electrical appliances, daily necessities, building materials and decoration. Because of corrosion resistance, impact resistance, aging resistance, abrasion resistance, fire prevention, outdoor use to maintain 15 years without discoloration and other properties, almost all commodities with this method to produce out of the label.
For example, when you open a cell phone case, you can see the label with barcode inside. Many labels require to withstand the test of time, long-term non-deformation, non-fading, not due to contact with solvents on the wear and tear, can not be deformed because of high temperature discoloration, etc., so it is necessary to use a special material printing media and printing materials to ensure that these characteristics, general inkjet, laser printing technology is not achievable.
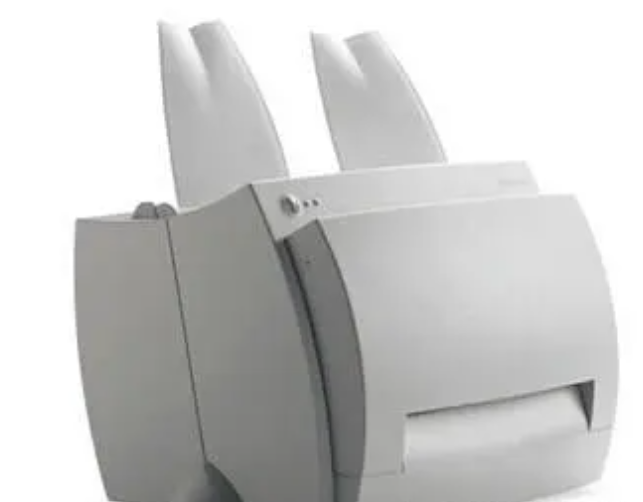
Eleventh, Sandblasting
Sandblasting in the application of metal surface is very common, the principle is to accelerate the abrasive particles to the metal surface impact, and to achieve rust removal, deburring, oxidation layer or surface pretreatment, etc., which can change the surface finish of the metal surface and stress state. Some of the parameters affecting the sandblasting technology need to be paid attention to, such as the type of abrasive, abrasive particle size, spray distance, spray angle and speed, and so on. In addition to sandblasting, shot blasting is also one of the good choices.
The sandblasting process can be divided into two kinds of air pressure spray gun and impeller shot blasting, and the advantage of sandblasting process is that it can remove the phi, remove the burrs after die-casting, stamping, flame cutting and forging, and the effect is better for the thinner workpieces and burrs with pores, and it can clean up the sand casting process of the residual sand particles, clean up the rust stains on the cast iron or steel, clean up the removal of oxidized skin after the heat treatment, burnishing, forging, rolling and other thermal processes.
In addition, for coating applications, it removes existing paint or protective coatings, covers defects such as cracks or cold streaks on castings, and provides a glossy surface. Coupled with surface stress, it provides a consistent roughened, oiled and painted surface, and in highly stressed metal parts such as springs and connecting rods, deformation and strengthening occurs when the part is subjected to constant localized hammering. This peening effect requires the use of round abrasives, such as stainless steel shot, in a high-energy shot blasting machine or a specialized power blasting machine. To determine the surface hardening effect of a machine, the test piece can be shot peened or sandblasted and the amount of deformation can be measured to see if it meets the requirements.
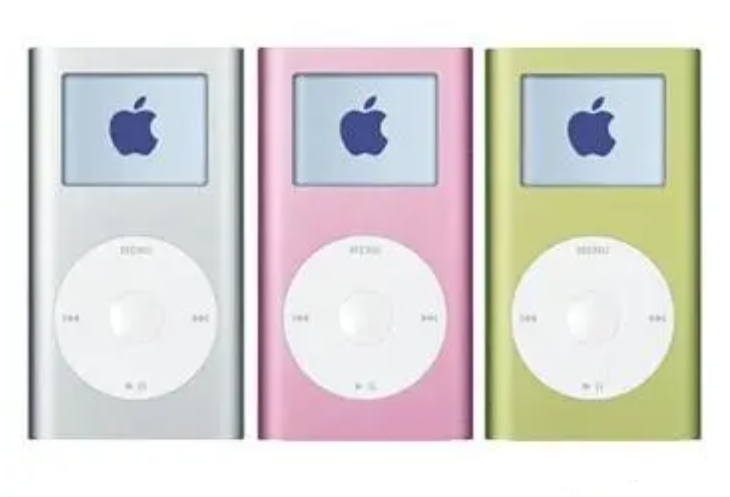
Twelfth, laser laser engraving
An optical principle of surface treatment process, cell phones and electronic dictionaries used on the keys. Simply put is this: for example, I want to do a keyboard, he has the word above, the word has blue, green, red and gray, the key body is white, laser engraving, the first spray oil, blue, green, red, gray spray the corresponding color, pay attention to do not spray to the other keys, so that looks like the blue keys, green keys keys, and so on, and then the whole of the spray a layer of white, so that it is a whole piece of white keyboard, the blue and green are wrapped underneath. are wrapped in the following.
At this point you can laser engraving, the use of laser technology and ID out of the key map made of film, carve off the top white oil, such as processing letter "A", carve off the strokes on the white, then under the blue or green will be exposed, so that the shape of the letter of the shape of the keys of a variety of colors.
At the same time, if you want to translucent, with PC or PMMA, spray a layer of oil, carve off the font part, then there is a light underneath the words will come out, but then we have to consider a variety of oil adhesion properties. Because each color key to spray different oil, so do the structure to take this into account, the key to separate points, so as to avoid spraying to unnecessary places, there is also a loss of large places as well as to do two or more, so that there can be more than one can be supporting.
The color difference of each color to be a little larger, the largest, such as black and white, so that the machine is easy to distinguish, but also carve clean, so as not to carve and not clean, affecting the appearance of the quality of the font of each different color do not lean too close.
Radium carving required paint and ordinary plastic shell spray paint composition is different, called double leaf paint, the texture is softer, suitable for carving. In addition, before spraying the appearance of paint to spray a layer of black on the surface of the raw material, otherwise the color is no way to carve off.
Usually laser engraving machine can engrave the following materials: bamboo wood products, plexiglass, metal plate, glass, stone, crystal, corian, paper, two-color plate, aluminum oxide, leather, plastic, epoxy resin, polyester resin, spray metal.
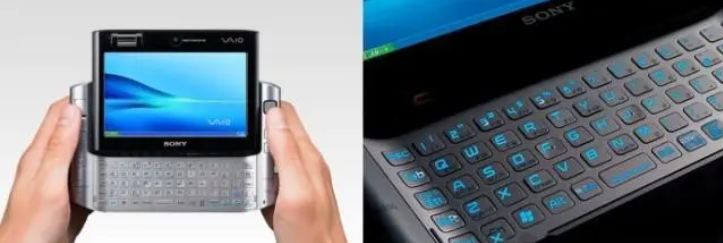
Thirteenth, screen printing - is a stencil with images or patterns are attached to the screen for printing.
(Applicable to flat surfaces, single surfaces, or surfaces with a small drop)
Usually the screen is made of nylon, polyester, silk or metal mesh. When the substrate is placed directly under the screen with a stencil, screen printing ink or paint in the squeezing of the squeegee through the middle of the screen mesh, printing to the substrate (squeegee manual and automatic two kinds).
Screen on the stencil to part of the screen small holes sealed so that the pigment can not pass through the screen, and only part of the image can pass through, so only the image on the substrate part of the print. In other words, screen printing is actually the use of ink penetration through the printing plate for printing, which is called it for screen printing and not called silk screen printing or silkscreen reasons, because not only silk used as a screen material, nylon, polyester, cotton fabrics, cotton, stainless steel, copper, brass and bronze can be used as screen material.
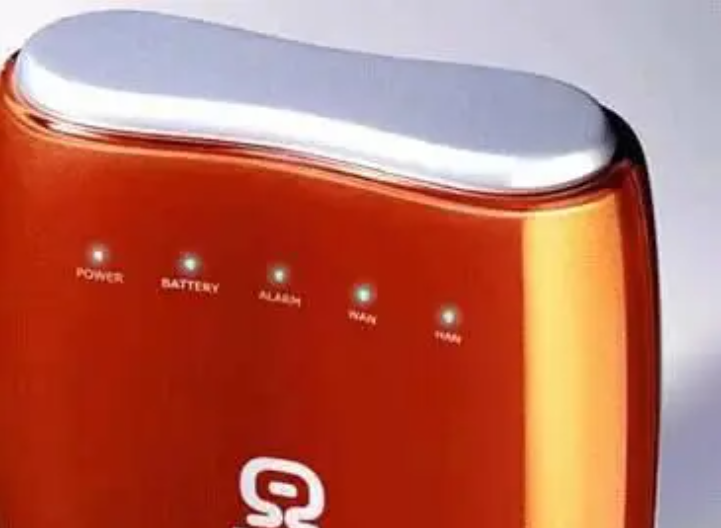
Fourteenth, ultrasonic welding
Is a high-tech technology to fuse ripe plastic plastic products, a variety of ripe plastic plastic parts can be used ultrasonic welding processing, without the need to add solvents, adhesives or other auxiliary products. The advantage is to increase productivity, reduce costs and improve product quality.
Ultrasonic plastic welding principle is generated by the generator 20KHZ (or 15KHZ) of high-pressure, high-frequency signals, through the transducer system, the signal is converted to high-frequency mechanical vibration, added to the plastic workpiece, through the surface of the workpiece and the intrinsic molecular friction and so that the transmission of the interface to the interface of the temperature rises when the temperature reaches the melting point of the workpiece itself, so that the interface quickly melted, and then fill the interface gap. When the vibration stops, the workpiece is cooled under a certain pressure to form a perfect weld.
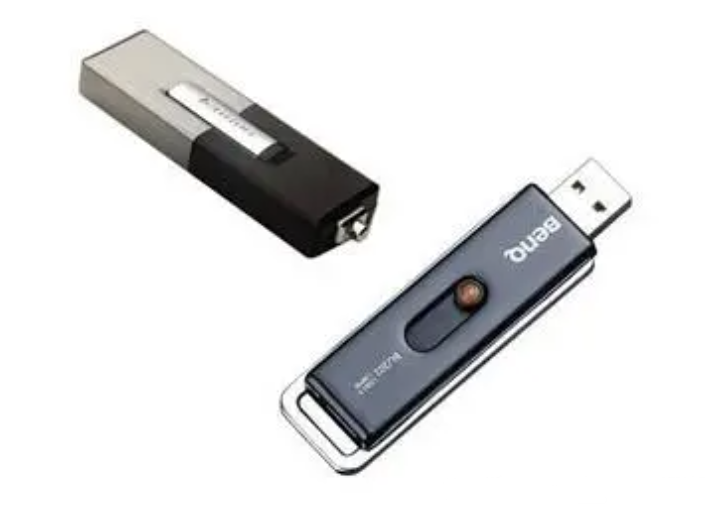
Fifteenth, pressure injection molding
Injection molding is also known as injection molding, which is a kind of injection and molding molding method. Injection molding method has the advantage of fast production speed, high efficiency, the operation can be automated, and can be molded in the shape of complex parts. The disadvantage is that the mold cost is high, and cleaning difficulties, so small quantities of products should not use this method of molding.
With this method of molding products are: television shells, semiconductor radio shells, electrical appliances on the connectors, knobs, coil skeleton, gears, automotive lampshades, tea cups, rice bowls, soap boxes, bathtubs, sandals and so on.
At present, the injection molding is applicable to all thermoplastics, its molding cycle is short, color variety, shape can be from simple to complex, size can be from large to small, and the product size is accurate, the product is easy to update.
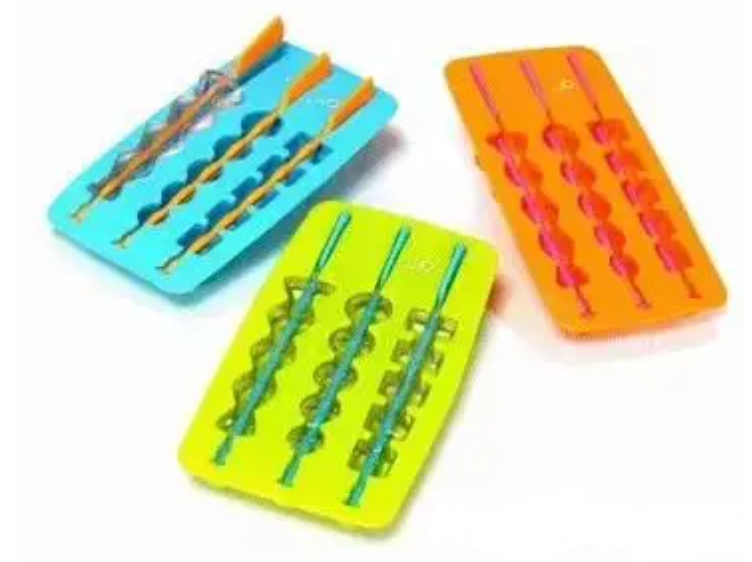
Sixteenth, two-color injection molding
Double shot molding mainly uses two tubes of double-shot molding machine with two sets of molds to make double-shot products through two molds in sequential order. Compared with traditional injection molding, double shot injection molding process has the following advantages:
1, The core material can use low viscosity material to reduce the injection pressure.
2, From the consideration of environmental protection, the core material can use recycled secondary material.
3, According to the different characteristics of use, such as thick parts of the finished skin material using soft materials, the core material using hard materials or core material can be used to reduce the weight of the foam.
4, you can use the lower quality of the core material to reduce costs.
5, the skin material or core material can use expensive and special surface properties, such as anti-electromagnetic interference, high conductivity and other materials to increase product performance.
6, the appropriate skin material and core material can reduce the molded product residual stress, increase mechanical strength or product surface properties.
7, produce products such as marble grain.
From the multi-color injection molding, dual-material co-injection molding characteristics and applications can be seen in the future there is a gradual replacement of the traditional injection molding process trend. Innovative injection molding technology not only improves the precision of the injection molding process and provides difficult process technology, but also opens up the scope of the injection molding process. Innovative injection molding equipment and processes are the only way to meet the demand for increasingly diverse, high-quality, and high-value-added products.
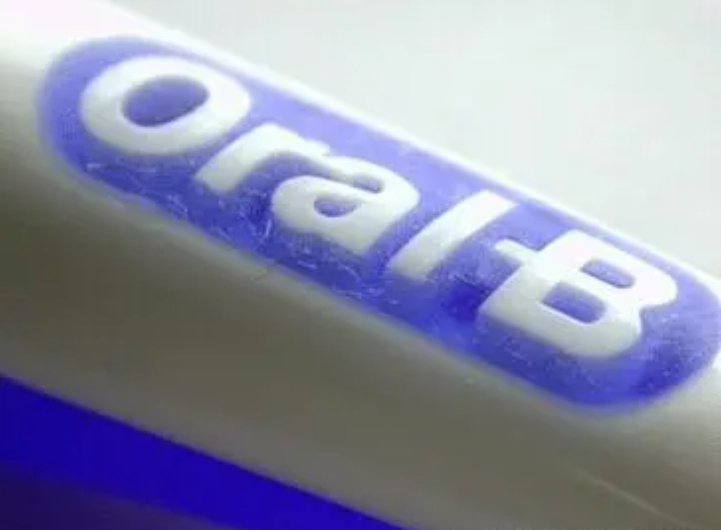
Seventeenth, blow molding
Blow molding - is by gas pressure to make the closed in the mold of the hot billet blown into a hollow product, or tube billet without mold blowing into a tube film method. This method is mainly used in the manufacture of various packaging containers and tubular films. Where the melt index of 0.04 ~ 1.12 are better hollow blow molding materials, such as polyethylene, polyvinyl chloride, polypropylene, polystyrene, thermoplastic polyester, polycarbonate, polyamide, cellulose acetate and polyacetal resin, etc., of which polyethylene has been applied to the most.
1, injection blow molding - injection molding method will first be made of plastic with the bottom of the blank, and then the blank will be moved to the blow mold blown into a hollow product.
2, extrusion blow molding - with the extrusion method will first be made of plastic bottomed billet, and then the billet will be moved to the blow mold blown into hollow products.
Injection blow molding and extrusion blow molding is the difference between the method of manufacturing blanks, blow molding process is basically the same.
Blow molding equipment in addition to the injection machine and extruder, mainly blow mold with the mold. Blow molds are usually composed of two flaps, which are equipped with coolant channels, parting surface holes can be inserted into the pressurized gas blow pipe.
3, stretch blow molding - stretch blow molding is a biaxial directional stretching of a blow molding, its method is the first billet for longitudinal stretching, and then blow with compressed air to achieve transverse stretching. Stretch blow molding can make the transparency, impact strength, surface hardness and rigidity of the products have been greatly improved, applicable to polypropylene, polyethylene terephthalate (PETP) blow molding.
Stretch blow molding including: injection billet directional stretch blow molding, extrusion billet directional stretch blow molding, multi-layer directional stretch blow molding, compression molding directional stretch blow molding.
4, blown film method - a method of molding thermoplastic film. Extrusion method will be extruded into a tube of plastic, and then with the help of the air blown into the tube to make it expand continuously to a certain size of the tubular film, after cooling, folded and wound into a double-layer flat film. Plastic film can be manufactured in many ways, such as blow molding, extrusion, casting, calendering, casting, etc., but the blow molding method is the most widely used. This method is suitable for the manufacture of polyethylene, polyvinyl chloride, polyamide and other films.
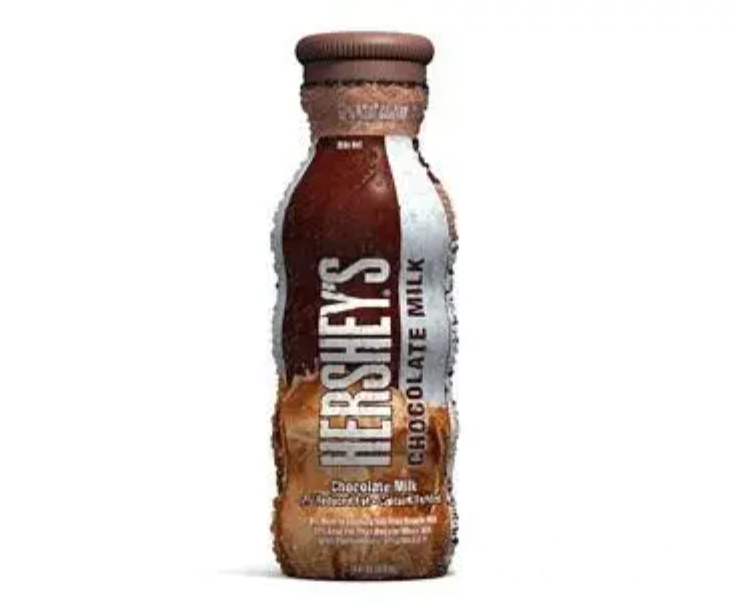
Ejghteenth, Stamping
Stamping is a pressure processing method in which a mold mounted on a press is used to apply pressure to the material at room temperature to produce separation or plastic deformation to obtain the desired part.
Characteristics of stamping processing:
1, stamping productivity and material utilization rate is high.
2, the production of parts of high precision, high complexity, high consistency.
3, high precision molds, high technical requirements, high production costs.
Material for stamping:
The shapes of materials used for stamping include plates, strips and blocks of various specifications. The size of plate material is larger, generally used for large parts stamping, for small and medium-sized parts, most of the plate material is cut into strips and then used.
Strip (also known as coil) has a variety of specifications of the width of the unfolding length of up to several thousand meters, suitable for mass production of automatic feeding, the material thickness is very small is also made into a strip supply. Block material is only used for the stamping of a few steel grades and expensive non-ferrous metals. Stamping commonly used materials are: ferrous metals: ordinary carbon structural steel, high-quality carbon steel, alloy structural steel, carbon tool steel, stainless steel, electrical silicon steel and so on.
Stamping process:
1, stamping processing due to the shape of the parts, size and precision of the different processes used are different.
2, According to the deformation characteristics of the material, the cold stamping process can be divided into two categories: separation process and forming process.
Separation process - refers to the blank under the action of stamping pressure, the deformation of the part of the stress reaches the limit of strength ob, so that the blank fracture and produce separation. Separation process mainly includes shearing and punching.
Forming process - refers to the blank under the action of stamping pressure, the deformation of the part of the stress reaches the yield limit os, but does not reach the strength limit. Make the blank produce plastic deformation, become a certain shape, size and accuracy of the processing process. Forming processes mainly include bending, deep drawing, flanging, spinning and so on.
If you have rapid prototype / mould customization needs,please contact us!
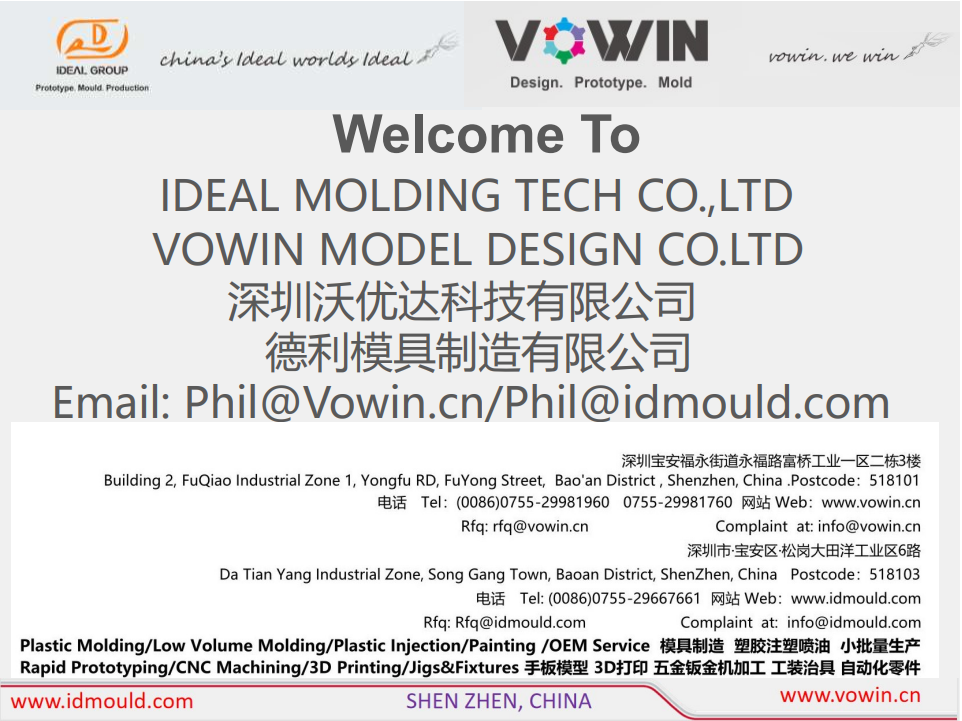
Posts by Topic
Recent Posts
- What do we need to pay attention to the plastic mold machining process and machining procedures?
- What kinds of plastic mold materials?
- What is the process of mold manufacturing?
- What should be paid attention to the polishing of injection molds?
- What is easy to ignore when maintaining and overhauling injection molds?
- What are the 6 systems of plastic molds?
- What are the methods of strengthening the surface of injection molds?
- What are the methods of insulation for injection molds?
- How to solve the problem of injection mold release difficulty?
- How can we increase the brightness of ABS injection molded parts?